Selective Laser Sintering (SLS) 3D printing services
High-quality prototypes and manufacturing parts.
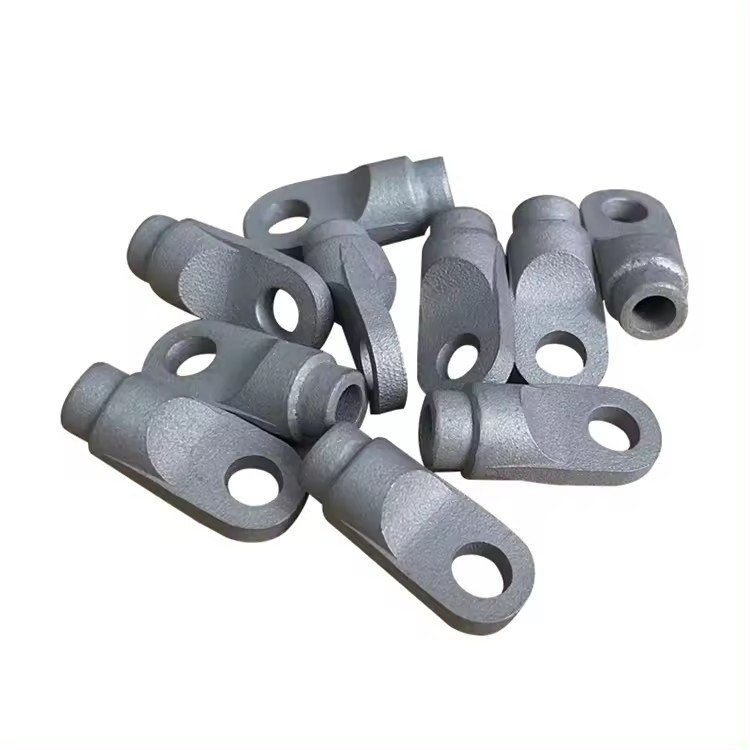
Selective Laser Sintering (SLS) 3D Printing Service
What is SLS 3D printing?
Selective laser sintering, also known as SLS printing, is an advanced additive manufacturing technology that enables the production of precise and long-lasting parts suitable for direct use in end-use applications, low-volume production, or rapid prototyping. SLS printing is a cost-effective solution for industrial 3D printing services as it allows for the bulk production of parts without the need for support structures. The primary materials used in SLS printing are nylon, which can be infused with different fillers to enhance their properties, ranging from rigid carbon-filled to flame retardant options.

Selective laser sintering is a layer-based additive manufacturing technology that utilizes a high-power laser, such as a carbon dioxide laser, to fuse small particles of plastic powders together, forming a solid object with a desired three-dimensional shape. This process involves scanning cross-sections of the object, which are generated from a 3-D digital description (such as a CAD file or scan data), onto a powder bed. After each cross-section is scanned, the powder bed is lowered by one layer thickness, a new layer of material is added on top, and the selective laser sintering process is repeated until the entire object is fully formed.
SLS Materials
Selective Laser Sintering 3D Printing Materials
Material | Other Common Names | Shore Hardness | Elongation at Break (%) | Impact Strength, Notched (kJ/m²) | |
---|---|---|---|---|---|
Nylon 12 | Durable plastic, PA12, PA 2200 | 75D | 18% | 4.8 kJ/m² | |
Nylon 12, Glass-filled (GF) | Stiff plastic, PA12 GF, PA 3200 GF | 80D | 9% | 4.2 kJ/m² | |
Nylon 11 EX | Ductile plastic, PA11, RilsanĀ® Invent Natural | 77D | 45% | No break | |
Nylon 12, Carbon-Filled (CF) | High-performance plastic, carbon-filled PA12, PA 602-CF, carbonmide | N/A | 4% | 5.3 kJ/m² | |
Nylon 12, Aluminum-Filled (AF) | Metallic gray plastic, aluminum-filled PA12, alumide | 76D | 3% | 4.6 kJ/m² | |
Nylon 12, Mineral-Filled (HST) | Heat-resistant plastic, mineral fiber-reinforced PA12, PA 620-MF | 75D | 3-5% | N/A | |
Nylon 12, Flame Retardant (FR) | Meets the FAR 25.853 60 second burn specification, PA 606-FR | 73D | 24% | N/A |
SLS General Tolerances
Description | Tolerance Notes |
---|---|
General Tolerances | SLS Nylon 12 and variants are ± 0.015ā, or ± 0.002″ per inch, whichever is greater.*SLS Nylon 11 and variants are ± 0.020ā, or ± 0.003″ per inch, whichever is greater.**Results are typical. |
Build Area | Build area up to 13″ x 13″ x 20″. Glass filled can extend up to 26″ x 15″ x 23″. |
Minimum Feature Size | 0.030″ or greater. |
Standard Layer Thickness | 0.0045″ |
The chart illustrates the standard tolerances for selective laser sintering. Variations in tolerances and flatness may occur due to stresses during the manufacturing process and other geometric factors. Components with thicker geometries, flat or wide surfaces, and uneven wall thicknesses are more likely to experience significant deviations or warping. Enhanced tolerances can potentially be achieved through a manual quotation review following the successful completion of a prototype build, and will need to be approved on a case-by-case basis. The general tolerances are applicable prior to any secondary finishing or post-processing, unless specified otherwise. For further details on tolerances specific to each process, please refer to MXY’s Manufacturing Standards.
SLS Applications
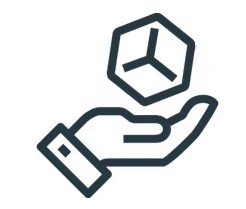
Models Depicting Concepts
Product developers can easily produce physical prototypes of their designs using plastic 3D printing, thanks to its speed and versatility in the iterative process.
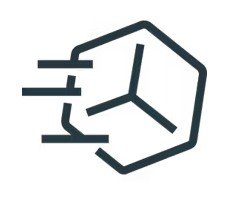
Rapid Prototyping
Plastic 3D printing enables the production of functional plastic prototypes, including moving parts and all-in-one assemblies.
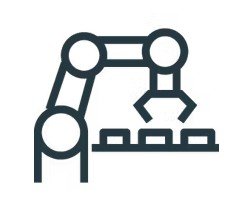
Digital Production Directly
Plastic 3D Printing is perfect for creating numerous customized or individual parts due to its exceptional precision and reliability.
SLS Finishes
Standard
SLS parts undergo a sandblasting procedure and manual powder elimination to remove excess powder. In cases where it is feasible, internal holes can be drilled to the required dimensions. The final appearance of the parts is a smooth white matte finish, resembling fine sugar cubes.
Dyed in Color
The available color choices for dye include black, blue, green, red, and yellow. However, it is important to note that there may be slight variations in consistency from one batch to another, with black being the most consistent option. The dye is capable of penetrating approximately 0.010 inches deep.
The media plummeted
The parts undergo abrasive media tumbling after the standard finish, resulting in minimized grow lines and potentially softened sharp edges. This process leaves the parts with a smooth eggshell finish.
Vapor Smoothing
The AMT PostPro3D is an automated post-processing technology that delivers a superior surface finish. Through vapor smoothing, surfaces are transformed from matte to semi-gloss, while also sealing the surface, improving mechanical properties, and ensuring a uniform cosmetic finish suitable for production. Additionally, parts that have undergone vapor smoothing can be dyed.
Nickel plating
Nickel plating involves a standard finish that incorporates a secondary copper + nickel plating method, resulting in a nickel coating of 0.004″-0.006″ thickness. This process enhances the durability, stiffness, and wear resistance of the material, although it is not primarily intended for cosmetic purposes. The resulting finish is characterized by a rough nickel texture.
Extra Coatings
MXY provides supplementary SLS finishing and customization choices upon inquiry.
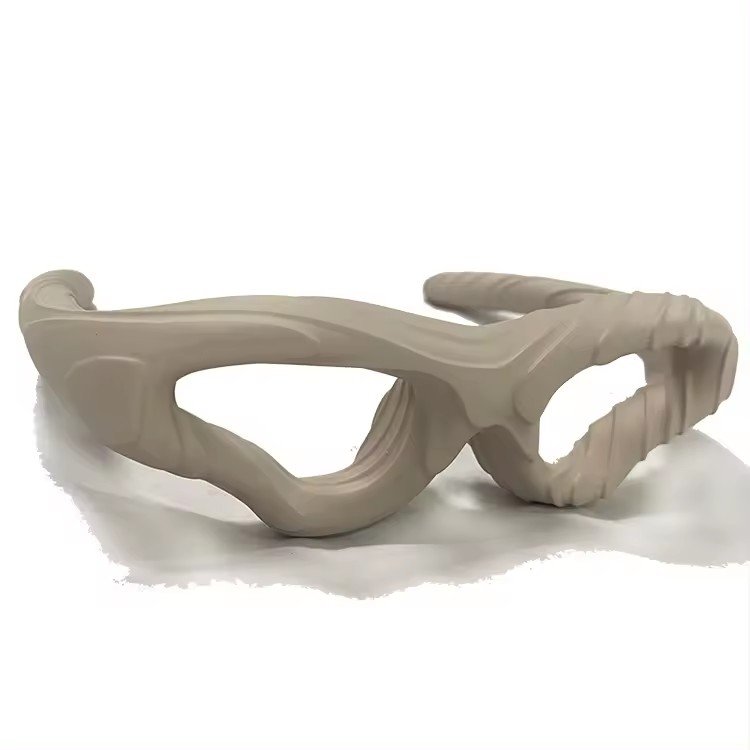
Benefits of Selective Laser Sintering (SLS) 3d printing
Why choose mXY

Endless choices
Select from a wide range of options for your order, including various materials, finishes, tolerances, markings, and certifications.

User-friendly
Have your parts conveniently delivered to your doorstep, eliminating the need for sourcing, project management, logistics, or shipping.
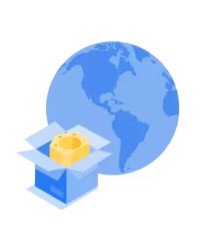
Verified Network
Our certifications include ISO 9001:2015, ISO 13485, and AS9100D. Only the best shops that meet our standards become Suppliers.
Advantages of SLS 3D Printing
It is capable of producing parts using various SLS materials such as plastic, metal, ceramic, or glass powder, which contributes to its popularity as a machining process. Unlike other 3D printing technologies, SLS does not necessitate a support structure, allowing for the production of larger quantities of parts with reduced labor and material costs. Moreover, the absence of support structure removal minimizes the risk of damaging the intricate internal geometries achievable through 3D manufacturing.
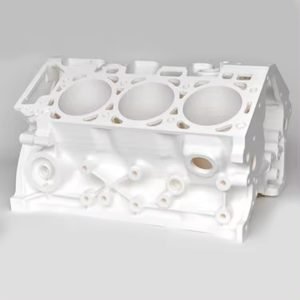
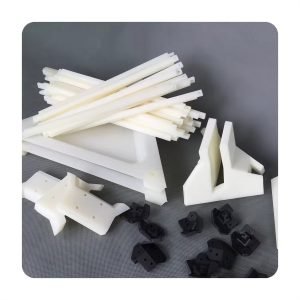
SLS offers benefits for both the swift creation of prototypes and the production of functional end-use parts in small quantities. Notably, nylon is a resilient material that possesses excellent impact strength, moderate flexibility, and remarkable resistance to environmental elements. Moreover, SLS nylon material has obtained FDA approval and USP Class VI/121C certification for skin contact. The amalgamation of intricate designs, adaptable material options, quick production cycles, and exceptional durability has propelled the growing popularity of SLS across various industries.