HP Multi Jet Fusion
High-quality prototypes and manufacturing parts.

Services for HP Multi Jet Fusion (MJF) 3D Printing
What is HP MJF 3D printing?
The HP Multi Jet Fusion (MJF) technology is renowned for its ability to produce highly accurate and durable parts at fast speeds. In comparison to other powder bed fusion technologies like selective laser sintering (SLS) or direct metal laser sintering (DMLS), MJF stands out due to its affordability, speed, and high resolution. This makes it an ideal choice for various applications such as end-use, low-volume production, rapid prototyping, or even as a bridge process to injection molding. By utilizing MJF, engineers can gain valuable insights into the performance of parts with minimal upfront costs.
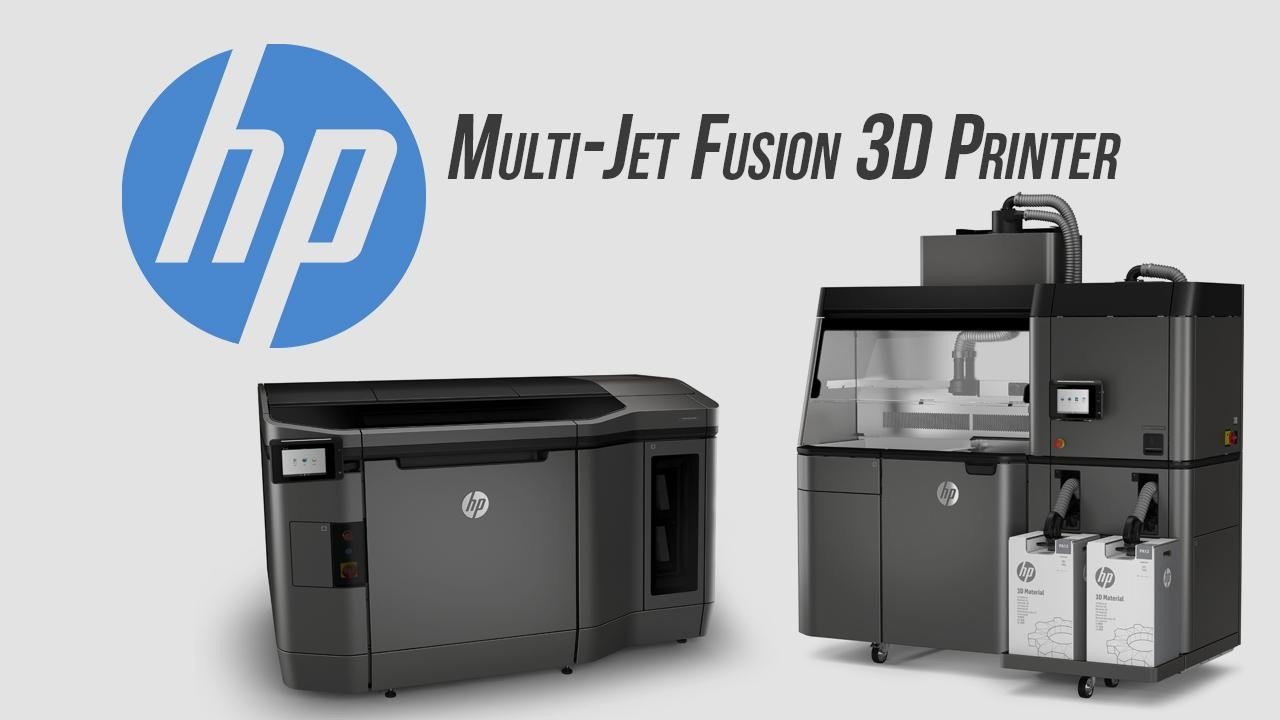
HP MJF Tolerances
Standard MJF tolerances determined by HP 5200-Series, Balanced Mode.
Material | Under 30 mm (1.2″) | 30 – 50 mm (1.2″ – 2.0″) | 50 – 80 mm (2.0″ – 3.2″) |
---|---|---|---|
Nylon 11 | XY = ± 0.30 mm / .012″; Z = ± 0.42 mm / .017″ | XY = ± 0.36 mm / .014″; Z = ± 0.62 mm / .024″ | XY = ± 0.44 mm / .017″; Z = ± 1.18 mm / .046″ |
Nylon 12 | XY = ± 0.25 mm / .010″; Z = ± 0.42 mm / .017″ | XY = ± 0.30 mm / .012″; Z = ± 0.50 mm / .020″ | XY = ± 0.37 mm / .015″; Z = ± 0.60 mm / .024″ |
Nylon 12, Glass-Filled | XY = ± 0.31 mm / .012″; Z = ± 0.43 mm / .017″ | XY = ± 0.35 mm / .014″; Z = ± 0.71 mm / .028″ | XY = ± 0.39 mm / .015″; Z = ± 1.16 mm / .046″ |
Polypropylene (PP) | XY = ± 0.30 mm / .012″; Z = ± 0.40 mm / .016″ | XY = ± 0.40 mm / .016″; Z = ± 0.65 mm / .026″ | XY = ± 0.45 mm / .018″; Z = ± 1.00 mm / .039″ |
TPU 88A (TPU01) | XY = ± 0.44 mm / .017″; Z = ± 1.05 mm / .041″ | XY = ± 0.52 mm / .020″; Z = ± 1.35 mm / .053″ | XY = ± 0.66 mm / .026″; Z = ± 1.80 mm / .071″ |
Results are based on a comprehensive tolerance study performed by HP.
HP Multi Jet Fusion Characteristics and Printing Capacity
Description | Tolerance Notes |
Build Area | Build area up to 15 x 11 x 15″ (14 x 11 x 13″ is the recommended usable area). |
Minimum Feature Size | 0.020″ (0.040″ recommended) or greater. |
Layer Thickness | 80 Microns (0.0031″) |
During the construction process and when considering the geometry, various stresses can lead to variations in tolerances and flatness. Parts that have thicker geometries, are flat or broad, or have uneven wall thicknesses are more likely to experience significant deviations or warping.
HP MJF Applications
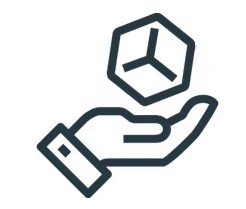
Models Depicting Concepts
Product developers can easily produce physical prototypes of their designs using plastic 3D printing, thanks to its speed and versatility in the iterative process.
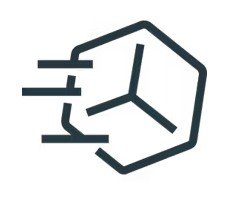
Rapid Prototyping
Plastic 3D printing enables the production of functional plastic prototypes, including moving parts and all-in-one assemblies.
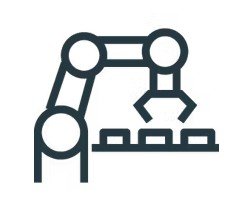
Digital Production Directly
Plastic 3D Printing is perfect for creating numerous customized or individual parts due to its exceptional precision and reliability.
MJF Printing Materials
HP MJF Materials Available
Material | Description | Shore Hardness | Elongation at Break (XY, ZX %) | Impact Strength (XY, ZX kJ/m²) | |
---|---|---|---|---|---|
Nylon 11 | HP 3D High Reusability PA 11 | 80D | 55%, 40% | 6 kJ/m², 5 kJ/m² | |
Nylon 12 | HP 3D High Reusability PA 12 | 80D | 20%, 15% | 3.6 kJ/m², 3.5 kJ/m² | |
Nylon 12, Glass-Filled | HP 3D High Reusability PA 12 Glass Beads (40% GB) | 82D | 10% | 3 kJ/m² | |
Polypropylene (PP) | HP 3D High Reusability PP | 70D (est.) | 20% | 3.5 kJ/m², 3.0 kJ/m² | |
TPU 88A | BASF Ultrasint™ TPU01 | 88A | 220%, 120% | Partial break, No break |

HP resources
Why choose mXY

Endless choices
Select from a wide range of options for your order, including various materials, finishes, tolerances, markings, and certifications.

User-friendly
Have your parts conveniently delivered to your doorstep, eliminating the need for sourcing, project management, logistics, or shipping.
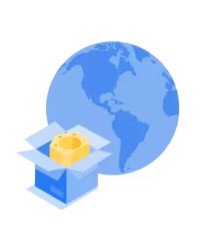
Verified Network
Our certifications include ISO 9001:2015, ISO 13485, and AS9100D. Only the best shops that meet our standards become Suppliers.
Benefits of MJF 3D Printing Technology
While there are numerous advantages to utilizing MJF printing, a few key benefits truly stand out. Firstly, the standard build parameters are optimized to achieve the highest density possible. As a result, Multi Jet Fusion parts are completely watertight. If you prefer SLS but require higher production quantities for small-batch runs, Multi Jet Fusion is the ideal choice. MJF printers have the capability to simultaneously print multiple parts across the entire build volume, allowing for printing speeds up to 10 times faster than SLS or other 3D printing methods. Additionally, Multi Jet Fusion offers more balanced mechanical properties across the X, Y, and Z axes when compared to SLS.
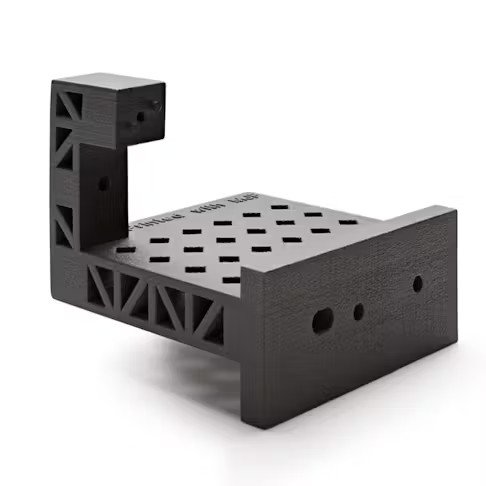
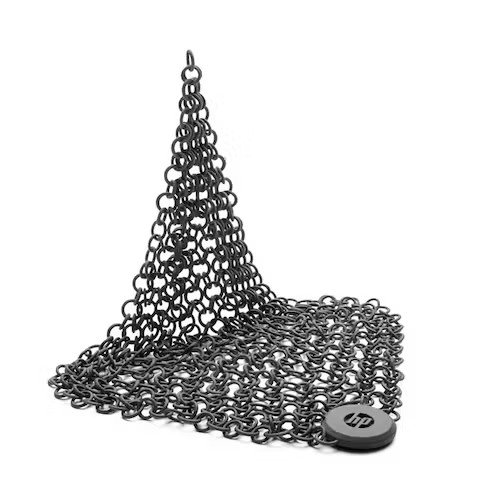
For those considering injection molding for their project, it is recommended to create a 3D printed “test” part before investing in metal molds. While SLA is excellent for producing highly detailed and high-resolution prints, the UV-cured resins used are not as durable as traditional thermoplastics. These prints can degrade when exposed to UV light and moisture. On the other hand, Multi Jet Fusion can produce extremely precise prints while maintaining the structural integrity of traditional thermoplastics, especially when utilizing glass-filled nylon. This makes it an excellent choice for testing fit and functionality before moving forward with injection molding.