PolyJet
Prototypes, models showcasing color concepts, and simulated overmold parts can be produced within a matter of days.

PolyJet 3D Printing Service
Stereolithography (SLA) is an advanced 3D printing technique renowned for its ability to create precise and detailed parts suitable for both end-use production and rapid prototyping. With a wide range of over 15 specially formulated SLA materials, Xometry empowers the development of market-ready products.


SLA Materials
SLA Materials Available we do
Material Name | Description | Flexural Strength (MPa/KSI) | Elongation at Break (%) | HDT@0.46 MPa (°C) | |
---|---|---|---|---|---|
Accura 25 | White, PP-like | 58 MPa/KSI | 20% | 63 °C | |
Accura ClearVue | Clear/Translucent, PC-like | 67 MPa/KSI | 7% | 46 °C | |
Somos WaterShed XC 11122 | Clear/Translucent, ABS-like | 69 MPa/KSI | 15% | 50 °C | |
Somos EvoLVe 128 | White, ABS-like | 70 MPa/KSI | 11% | 52 °C | |
Accura Xtreme Grey | Grey, ABS-like | 71 MPa/KSI | 22% | 62 °C | |
Somos NeXt | White, PP-like | 71 MPa/KSI | 10% | 57 °C | |
Somos ProtoGen 18420 | White, ABS-like | 71 MPa/KSI | 16% | 47 °C | |
Somos Taurus | Dark Gray, ABS-like | 74 MPa/KSI | 24% | 62 °C | |
Accura ABS Black (SL 7820) | Black (painted), ABS-like | 78 MPa/KSI | 13% | 51 °C | |
Accura Xtreme White 200 | White, ABS-like | 79 MPa/KSI | 20% | 47 °C | |
Somos WaterClear Ultra 10122 | Clear/Translucent, PC-like | 84 MPa/KSI | 7% | 47 °C | |
Accura 60 | Clear/Translucent, PC-like | 101 MPa/KSI | 13% | 55 °C | |
Somos ProtoTherm 12120* | Translucent Red, PC-like | 109 MPa/KSI | 4% | 126 °C | |
Somos PerFORM* | White, Ceramic-filled | 146 MPa/KSI | 1% | 268 °C | |
Accura Bluestone* | Blue, Ceramic-filled | 154 MPa/KSI | 2% | 284 °C |
*Requires post-thermal curing to achieve HDT.
SLA Standard Tolerances
Description | Standard Resolution | High Resolution |
---|---|---|
Build envelope | 29ā x 25ā x 21ā | 10ā x 10ā x 10ā |
Layer height | 0.004″ | 0.002″ |
Tolerance, XY Plane | +/- 0.005ā for the first inch is typical, plus +/- 0.002ā for every inch thereafter. | +/- 0.005ā for the first inch is typical, plus +/- 0.002ā for every inch thereafter. |
Tolerance, Z Plane | +/- 0.010ā for the first inch is typical, plus +/- 0.002ā for every inch thereafter. | +/- 0.010ā for the first inch is typical, plus +/- 0.002ā for every inch thereafter. |
Minimum linear feature size | Under 0.030ā are at risk and under 0.020ā will not build. | Under 0.020ā are at risk and under 0.010ā will not build. |
Minimum radial feature size | 0.035″ | 0.030″ |
The information provided in the table outlines the standard tolerances for industrial-grade stereolithography (SLA) services. Variations in tolerances and flatness may occur due to factors such as stresses during the build, support strategy, and geometry considerations. Enhanced tolerances can potentially be achieved through a manual quote review following the successful completion of a prototype build, subject to approval on a case-by-case basis. These general tolerances are applicable prior to any secondary finishing or post-processing, unless stated otherwise. For further details on tolerances specific to each process, please refer to Xometry’s Manufacturing Standards.
SLA Applications
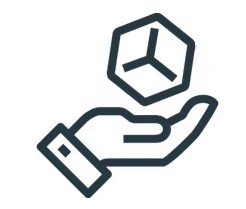
Models Depicting Concepts
Product developers can easily produce physical prototypes of their designs using plastic 3D printing, thanks to its speed and versatility in the iterative process.
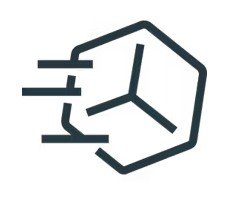
Rapid Prototyping
Plastic 3D printing enables the production of functional plastic prototypes, including moving parts and all-in-one assemblies.
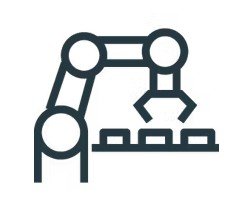
Digital Production Directly
Plastic 3D Printing is perfect for creating numerous customized or individual parts due to its exceptional precision and reliability.
SLA Finishes
Flat (Regular)
The supported surfaces will be lightly sanded using either 220 or 320 grit sandpaper, and then media blasted to create a uniform matte finish.
Organic
The surfaces that are supported will undergo a light sanding process using either 220 or 320 grit sandpaper to enhance the quality of the surface. Scratches from sanding will be apparent on the supported surfaces.
The media plummeted
The parts undergo abrasive media tumbling after the standard finish, resulting in minimized grow lines and potentially softened sharp edges. This process leaves the parts with a smooth eggshell finish.
Strips
Supported areas may exhibit tiny grid-like dots or surface imperfections due to the removal of support structures.
Rapidly Transparent
Accura ClearVue is exclusively compatible. Only surfaces that have been sanded are supported. The layering will remain visible on the parts. To enhance the inherent clarity, a high gloss clear coat is applied.
Customized
MXY offers a variety of supplementary SLA finishing choices, such as sanding, polishing, painting, post thermal processing, and plating, in order to cater to your specific requirements.
Why choose mXY

Endless choices
Select from a wide range of options for your order, including various materials, finishes, tolerances, markings, and certifications.

User-friendly
Have your parts conveniently delivered to your doorstep, eliminating the need for sourcing, project management, logistics, or shipping.
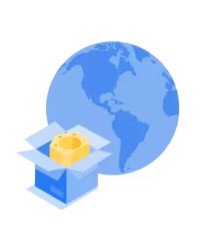
Verified Network
Our certifications include ISO 9001:2015, ISO 13485, and AS9100D. Only the best shops that meet our standards become Suppliers.
The Mechanism of Stereolithography
Stereolithography, also known as SLA, is an additive manufacturing process that uses UV light to solidify liquid photopolymer resin layer by layer. The resin is selectively cured to match the CAD design, and support structures are removed after printing. Xometry’s SLA printing service provides high-resolution printing for parts with fine details and surface finishes, making it a versatile option for custom parts in prototype and production settings.

Applications of SLA
SLA technology provides a diverse selection of materials and fast production times for complex net-shapes, making it an essential tool for a wide range of manufacturing sectors. It is predominantly used in the automotive industry to create intricate parts with various surface finishes. These parts can be embossed or engraved, with options for matte, natural, and other finishes depending on manufacturing requirements. While stereolithography has excelled in rapid prototyping and design support for automotive applications, it is now gaining traction in various mechanical modeling sectors on a larger scale.