Plastic Injection Molding Services
Get your Injection Molding prototypes and production parts delivered within days

Custom Plastic Injection Molding Services
MXY custom plastic mold service provides on-demand prototype and production molding. Our commitment to prioritizing our customers guarantees the delivery of high-quality services while maintaining exceptional design standards, all at a competitive price. Consultation from our team of experts is available for every injection mold quote, with project managers overseeing every order to facilitate the transition from design to production. The team has extensive experience across various industries, including medical injection molding and liquid silicone rubber molding.
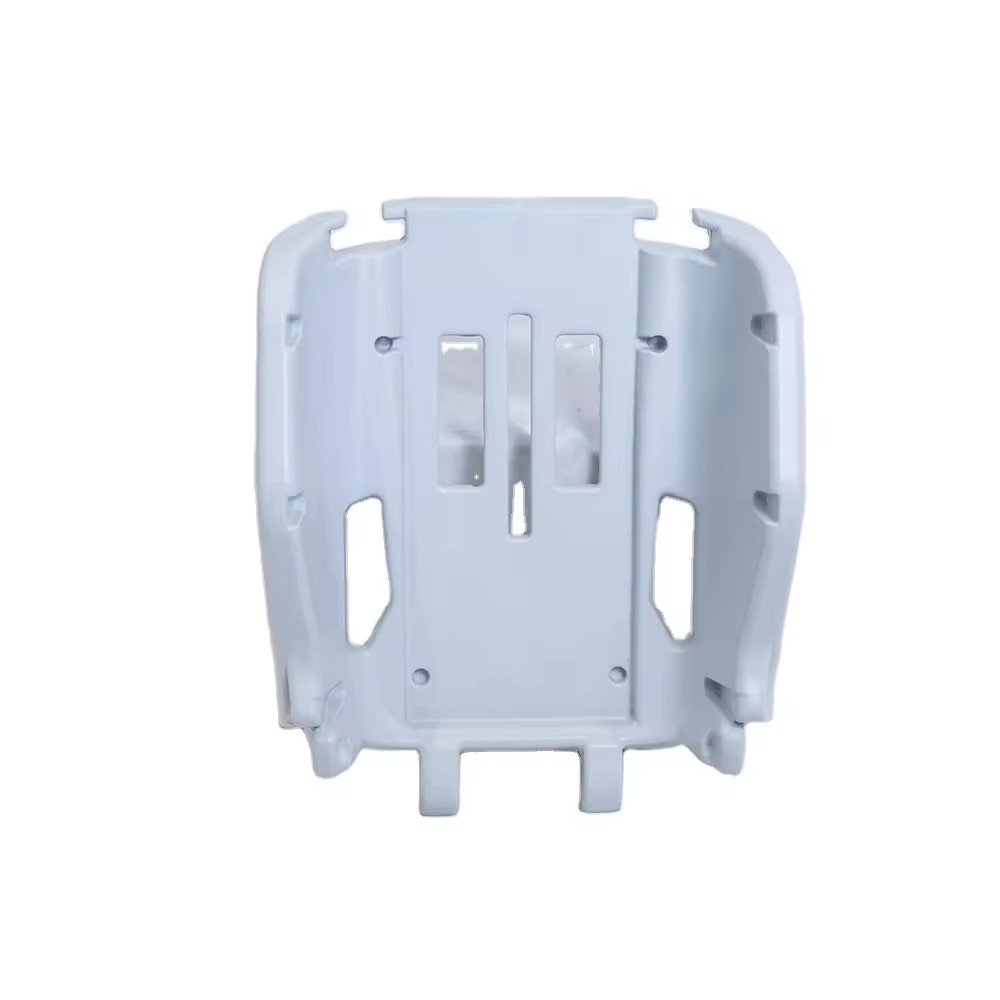
Injection Molding Mold Clasification
The Plastics Industry Association, previously known as the Society of Plastics Industry or SPI mold classifications, has established a comprehensive system of mold standards. These standards are divided into five classifications, ensuring that quotes and orders are efficiently processed and comply with consistent mold class categories.
Clasification | Manufacturing Standard | Cycles | Applications | Cost |
---|---|---|---|---|
Class 101 Mold | Exceptionally high output | 1 million or above | Exceptionally high output levels and rapid turnaround times | Highest-cost with finest quality materials |
Class 102 Mold | Medium to high | Less than one million. | Ideal for components made from abrasive materials and/or requiring precise tolerances | Fairly high priced with high quality materials |
Class 103 Mold | Medium | Less than 500,000 | Widely preferred mold for producing low to medium production parts | Within the standard price range |
Class 104 Mold | Low | Less than 100,000 | Suitable for small-scale manufacturing of parts using non-abrasive materials | Affordable price ranges |
Class 105 Mold | Very low | Less than 500 | Just a prototype | Inexpensive and limited production or prototypes |
Our Injection Molding Capabilities
Services | Details |
---|---|
Materials | Our inventory boasts a massive selection of plastic materials available for immediate purchase. |
Choices for Inspection and Certification | Incorporates FAI and PPAP. Compliant with ISO 9001, AS9100, ISO 13485, UL, ITAR, as well as ISO 7 and 8 standards for Medical Clean Room molding. |
Mold Cavity Tolerances | Tolerance of ± 0.004″ is applied during the mold machining process, with an added tolerance of ± 0.002″ per inch accounted for when considering shrinkage. |
Mold Ownership | Mold maintenance for customer-owned equipment is provided. |
Key Feature Tolerances | Requesting tighter tolerances can lead to an increase in tooling costs due to the need for additional sampling and grooming. We ensure that critical features are milled to a steel-safe condition. |
Reproducibility of Parts Alignment | +/- 0.003″ or lower |
Key Feature Tolerances | Requesting tighter tolerances can lead to an increase in tooling costs due to the need for additional sampling and grooming. We ensure that critical features are milled to a steel-safe condition. |
Types of Mold Available | MXY generally manufactures tools in Class 102, 103, and 104, with production grades spanning from Class 105 to Class 101, which is the highest production mold available for steel and aluminum. |
Custom plastic Injection Molding Materials
Inflexible Plastic Materials:
- ABS (acrylonitrile butadiene styrene): A high-strength general-purpose engineering plastic used in various commercial products.
- ASA (acrylonitrile styrene acrylate): Similar to ABS but with higher resistance to fading, making it suitable for outdoor use.
- CA (cellulose acetate): A flexible clear material commonly used in eyeglasses and film, and can be used in food contact.
- HDPE (high-density polyethylene): Known for its excellent strength-to-weight ratio and chemical resistance. Used in fuel tanks, connector insulators, and food containers, as well as outdoor equipment like playgrounds.
- LCP (liquid crystal polymer): Provides exceptional features for micromolding and thin-walled components, with mechanics even at elevated temperatures. Popular for electrical connectors, interconnects, and medical devices.
- LDPE (low-density polyethylene): A flexible and tough material with lower density compared to HDPE. Does not react to acids, bases, or alcohols. Useful for trays, snap lids, and general-purpose containers.
- PA 6 (polyamide 6, nylon 6): Offers increased mechanical strength, rigidity, good stability under heat, and/or chemical resistance.
- PA 6/6 (polyamide 6/6, nylon 6/6): Similar to PA 6, offering increased mechanical strength, rigidity, good stability under heat, and/or chemical resistance.
- PARA (polyarylamide): Often combined with infills like glass or mineral fibers, PARA creates rigid parts with low creep and slower water absorption than nylon (PA). Excellent for structural components in handheld and medical electronics.
- PBT (polybutylene terephthalate, Valox): A common electronic insulator with a polyester base. Widely used in automotive as a longer-wearing alternative to nylon.
- PBT-PET (polybutylene terephthalate-polyethylene terephthalate): A compounded blend of PBT and PET.
- PC (polycarbonate): A lightweight, glass-like plastic that is clear or colored. Highly utilized across multiple industries due to its impact resistance and durability.
- PC-ABS (polycarbonate-acrylonitrile butadiene styrene): A high-strength engineering thermoplastic with more flexibility than standard polycarbonate.
- PC-PBT (polycarbonate-polybutylene terephthalate, Xenoy): A tough and rigid material resistant to lubricants, solvents, and cleaning agents commonly used in electronic enclosures.
- PC-PET (polycarbonate-polyethylene terephthalate): A blend of PC and PET that provides tough and chemically resistant results, suitable as an alternative to PC-ABS. Ideal for sports equipment and healthcare applications.
- PCT (polycyclohexylenedimethylene terephthalate): A thermoplastic polyester with lower moisture absorption and better environmental stability than PET. Often used for connectors and switches.
- PE (polyethylene): One of the most common plastics with high ductility, abrasion resistance, and chemical resistance. Used in packaging, tubing, films, bottles, and more.
- PEEK (polyether ether ketone): Offers excellent tensile strength, making it a lightweight substitute for metal parts in high-temperature, high-stress applications. Resistant to chemicals, wear, and moisture.
- PEI (polyetherimide, Ultem): Known for its extremely high heat and flame resistance, PEI is commonly used in medical applications and is more affordable than PEEK.
- PE-PP (polyethylene-polypropylene): A resin blend of polypropylene and polyethylene.
- PE-PS (polyethylene-polystyrene): A resin blend of polyethylene and polystyrene.
- PE-PS (polyethylene-polystyrene): A resin blend of polyethylene and polystyrene.
- PES (polyethersulfone): A rigid, transparent plastic that is chemically inert, biocompatible, and sterilizable. Suitable for food-contact devices, aerospace, and automotive applications with high chemical exposure.
- PET (polyethylene terephthalate, Rynite):PETE is a transparent, durable, and lightweight PE resin widely utilized in food packaging, soda bottles, and jars. It is considered safe for food contact. PET is also recyclable with a resin code of.
- PLA (polylactic acid):PLA is a biodegradable and renewable plastic. It has a relatively low glass transition temperature and is commonly used in short-term applications.
- PMMA (polymethyl methacrylate, acrylic):
- PMMA is a transparent plastic with glass-like properties. It has excellent resistance to wear and tear, making it suitable for outdoor use.
- POM (acetal polyoxymethylene, Delrin):
- POM exhibits good moisture resistance, high wear-resistance, and low friction properties.
- PP (polypropylene):
- PP has outstanding electrical properties and minimal moisture absorption. It can withstand light loads over extended periods in varying temperatures. PP is often molded into parts requiring chemical or corrosion resistance.
- PPA (polyphthalamide):
- PPA is a subset of nylons (polyamide) that typically has a higher melting point and lower moisture absorption. It is commonly used in automotive and industrial applications due to its ability to withstand harsh chemicals. PPA is particularly suitable for fuel and fluid manifolds, as well as headlight housings.
- PPS (polyphenylene sulfide, Ryton):
- PPS is a high-performance thermoplastic known for its exceptional resistance to solvents.
- PS (polystyrene):
- PS is a clear, rigid, and brittle material extensively used in food packaging, clamshell containers, and disposable cutlery.
- PS-PPE (polystyrene-polyphenyl ethers, Noryl):
- PS-PPE, also known as Noryl, exhibits high heat and flame resistance. It possesses high stiffness and tensile strength, even at elevated temperatures.
- PSU (polysulfone, Udel):
- PSU is a rigid, stiff, and transparent plastic that serves as a higher-performance alternative to polycarbonate.
- PVC (polyvinyl chloride, Shore D):
- PVC is a rigid, general-purpose plastic commonly found in plumbing, non-food packaging, and trimming applications.
- PVDF (polyvinylidene fluoride, Kynar):
A chemically inert, high-temperature material. Due to its low friction, PVDF is used in plumbing parts, bearings, chemical handling, electrical wire insulation, and tubing. - SAN (styrene acrylonitrile):
A polystyrene that is heat resistant and transparent. Due to its relationship with polystyrene, SAN is low cost and has enhanced clarity and shine. SAN is common in household goods, door handles, and kitchenware. - TPO (thermoplastic polyolefin):
A flexible plastic with good chemical resistance but lower temperature resistance compared to PP. - TPU (thermoplastic polyurethane (Shore D)):
A tough, highly abrasion-resistant resin that bridges the gap between rubbers and plastics. TPUs can be formulated to be rigid or elastomeric. TPU exhibits a high flex before break and is ideal for wheels and door panels.
Molded Elastomer and Rubber Materials
- EPDM, also known as ethylene propylene diene monomer rubber or Viton, is a highly durable rubber elastomer that offers exceptional heat resistance, chemical resistance, and moisture sealing properties. It is commonly used in automotive seals, gaskets, O-rings, and electrical insulators.
- PEBA, or polyether block amide, is a flexible and soft plastic or elastomer that finds applications in medical devices like catheters. PEBA foams are also used for padding, shoe insoles, and sports equipment. It is resistant to moisture and UV exposure.
- PVC, or polyvinyl chloride, is a versatile elastomer that has a soft rubber-like texture. It is commonly used in outdoor products, protective films, and mats. PVC requires plasticizers to enhance its flexibility from its typical rigid state. Additionally, it is flame retardant due to its self-extinguishing properties.
- TPE, or thermoplastic elastomer, is a broad category of elastomers that exhibit high flexibility and elasticity similar to thermosets. However, they can be processed like thermoplastics through molding. TPE encompasses various unique elastomer classes.
- TPU, or thermoplastic polyurethane, is a tough and highly abrasion-resistant elastomer that bridges the gap between rubbers and plastics. It can be formulated to be rigid or elastomeric. TPU is ideal for applications such as flexible tires, skateboard wheels, and weatherproof gaskets, offering high flex before break.
- TPV, or thermoplastic elastomer vulcanized rubber, also known as Santoprene, is an excellent elastomer known for its versatility. It offers temperature resistance, compression, and elasticity. TPV finds applications in various industries due to its wide range of properties.
- LSR, or liquid silicone rubber, is a versatile rubber material that offers food and biocompatibility, extreme heat resistance, and excellent flexibility. It is commonly used in medical devices, automotive components, aerospace applications, and consumer products. The molding process for LSR is specialized and differs from traditional injection molding techniques.

The Process of Custom Plastic Injection Molding
The plastic injection molding process is a sophisticated technique that involves the use of an injection molding machine, high-quality raw plastic material, and a precisely machined mold. The raw plastic material is carefully melted in the injection unit before being injected into the mold, typically made from durable steel or aluminum. Once inside the mold, the plastic material cools and solidifies, resulting in a flawless final plastic part.
At MXY, we carefully evaluate your online quote for plastic injection molding. We then engage in a consultation with you to ensure that your project requirements, lead time, and pricing align perfectly. Utilizing your 3D part data, we proceed to CNC machine a top-notch injection mold of exceptional quality. Once the mold is refined and given the green light, MXY commences production. Our expertise extends to molding a wide range of products and parts, spanning from the tiniest medical insert to large-scale automotive, aerospace, and defense components.
popular Injection Mold Finishes
No additional polishing or grinding will be done. The part will exhibit visible tooling marks.
VDI 3400 Surface Finish, also known as VDI surface finish, is the mold texture standard established by Verein Deutscher Ingenieure (VDI), the Society of German Engineers. It is typically achieved through EDM machining to create matte finishes ranging from fine to coarse.
We offer a variety of finishes to choose from, including matte, swirls, lines, and patterns. Our popular texture finishes consist of MoldTech MT11010, MoldTech MT11020, and MoldTech MT11030. If you have any specific textured finishes in mind, we can accommodate your request.
The Society of Plastics Industry (SPI) offers a wide range of finishes, ranging from Grade 3 diamond/high polish to 320 stone low polish. These finishes include SPI A-1, SPI A-2, SPI A-3, SPI B-1, SPI B-2, SPI B-3, SPI C-1, SPI C-2, SPI C-3, SPI D-1, SPI D-2, and SPI D-3.
The finish chosen by the moldmaker is usually SPI B-2, which may vary based on the geometry and drafts. The interior non-cosmetic surfaces are generally left as-machined.
We have the capability to install standard inserts in both UNF and metric sizes, which are widely used in various applications.
Pad printing is a method used for transferring a 2D image onto a 3D object.
Utilize engraving techniques to imprint part numbers, logos, and other relevant information onto your components.
MXY possesses the skill to put together and tag injection molded components. Please communicate your requirements with your sales representative.
Plastic Injection Molding usages
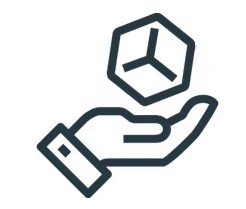
Models Depicting Concepts
Product developers can easily produce physical prototypes of their designs using plastic 3D printing, thanks to its speed and versatility in the iterative process.
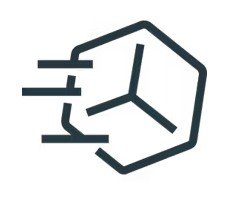
Rapid Prototyping
Plastic 3D printing enables the production of functional plastic prototypes, including moving parts and all-in-one assemblies.
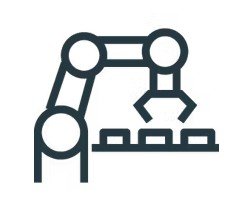
Digital Production Directly
Plastic 3D Printing is perfect for creating numerous customized or individual parts due to its exceptional precision and reliability.
Metal Sheet Fabrication Finishes
Why choose mXY

Endless choices
Select from a wide range of options for your order, including various materials, finishes, tolerances, markings, and certifications.

User-friendly
Have your parts conveniently delivered to your doorstep, eliminating the need for sourcing, project management, logistics, or shipping.
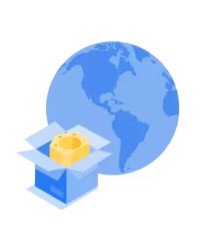
Verified Network
Our certifications include ISO 9001:2015, ISO 13485, and AS9100D. Only the best shops that meet our standards become Suppliers.
The process of placing an order with us
Submit CAD file
Please upload your part design securely to our online quoting tool.
Confirm specs
Customize your part specifications and choose a lead time that aligns with your timeline.
Receive instant quote
Lorem ipsum dolor sit amet, consectetur adipiscing elit. Aenean diam dolor, accumsan sed rutrum vel, dapibus et leo.
Manufacturing
Production kicks off right away
Quality assurance
We fully commit to ensuring that your parts are produced in accordance with our quality criteria.
Shipping
FAQ's
Explore our other production capacities

CNC Machining
Milling, Turning and Post Processing
Tolerances as low as ±.0008 in (0.020mm)
Lead durations 5 business days

3D Printing
FDM, SLA, SLS, MJF
± 0.3% starting from ± 0.3 mm (0.012 in)
Lead durations 1 business days

Injection Molding
Prototypes and production tooling
Diverse array of part intricacies and scales
1 to 2M parts