Fused Deposition Modeling
Superior Large-Scale FDM 3D Printing with Unmatched Quality.

3D Printing Service utilizing Fused Deposition Modeling (FDM)
What is FDM 3D printing?
Fused Deposition Modeling (FDM) is a well-known additive manufacturing technique recognized for its rapidity, precision, and cost-effectiveness. By precisely extruding molten material, FDM machines are capable of producing parts in a remarkably short period of time, sometimes even within a single day.
We provide FDM 3D printing services that feature expansive build volumes of up to 24ā³ x 36ā³ x 36ā³ on Stratasys Fortus platforms. This method offers a wide array of colors and a diverse selection of production-grade thermoplastics compared to other 3D printing processes. The materials available range from standard ABS or ASA to advanced options like polycarbonate and heat-resistant ULTEM.
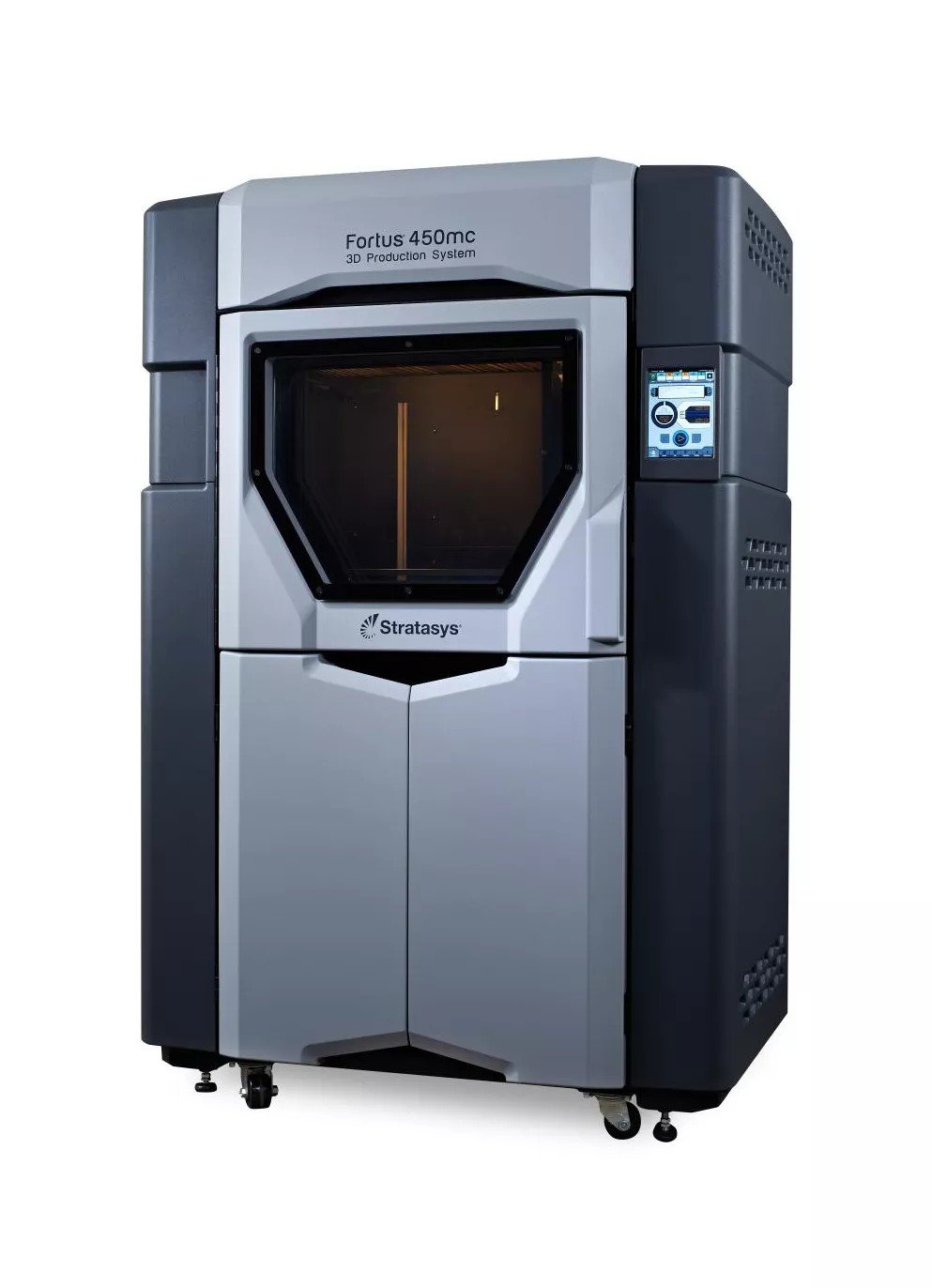
Finishing Options for FDM Parts
FDM Standard Tolerances
General Tolerances for FDM 3D Printing
Tolerance Note | Description |
---|---|
General Tolerance | +/- a single build layer thickness for the first inch and +/- .002ā for every inch thereafter. |
Build Size | Up to 24″ x 36″ x 36″ |
Layer Height, less than 16″ | 0.010″ Layers (0.008″ for PLA) |
Layer Height, greater than 16″ (up to 36″) | 0.013″ Layers |
Minimum Wall Thickness | 0.047″(less than 16″), 0.060″ (greater than 16″) |
Up to 24″ x 36″ x 36″ can be constructed with FDM 3D printing. parts up to 16″ can be produced by Stratasys Fortus 400/450-series machines, while parts larger than 16″ are produced by Stratasys Fortus 900MC or F900 platforms. With a build volume of 9.8″ x 8.3″ x 8.3, Prusa MK3S desktop FFF machines are used for PLA prototyping. Unless otherwise noted, general tolerances are applicable prior to secondary finishing or post-processing.

Fire-resistant Plastic 3D Printing
MXY’s 3D Print Service provides flame retardant polymers like FDM ULTEM 9085, FDM ULTEM 1010, and SLS Nylon 12, Flame Retardant, ideal for aviation and aerospace uses, meeting UL-94 V-0 and FAR 25.853 60 second burn test requirements.
Plastic 3D Printing Applications

Models Depicting Concepts
Product developers can easily produce physical prototypes of their designs using plastic 3D printing, thanks to its speed and versatility in the iterative process.

Rapid Prototyping
Plastic 3D printing enables the production of functional plastic prototypes, including moving parts and all-in-one assemblies.

Digital Production Directly
Plastic 3D Printing is perfect for creating numerous customized or individual parts due to its exceptional precision and reliability.
fDM 3D Printing Materials
Available FDM Materials
Material Name | Color(s) | Tensile Strength, Yield (XZ MPa-ZX MPa) | Elongation at Break (XZ%-ZX%) | HDT @ 66 psi (°C) | |
---|---|---|---|---|---|
ABS-M30 | Black, Blue, Dark Grey, Ivory, Red, White | 32 MPa-28 MPa | 7%-2% | 96 °C | |
ABS-ESD7 | Black (electrostatic dissipative properties) | 36 MPa | 3% | 96 °C | |
ABSi | Translucent Natural, Translucent Amber, Translucent Red | 37 MPa | 4.4% | 86 °C | |
ASA | Black, Dark Blue, Dark Gray, Light Gray, Green, Ivory, Orange, Red, White, Yellow | 27 MPa | 9%-3% | 98 °C | |
Nylon 12 | Black | 49.3 MPa-41.8 MPa | 30%-6.5% | 91.9 °C | |
PC-ABS | Black | 41 MPa | 6% | 110 °C | |
PC | White | 57 MPa-42 MPa | 4.8%-2.5% | 138 °C | |
PC-ISO | Translucent Natural, White | 57 MPa | 4% | 133 °C | |
PPSF | Tan | 55 MPa | 3% | 189 °C @ 264 psi | |
Prototyping PLA | Black, Blue, Red, White | 50 MPa-37 MPa | 2.9%-1.9% | 55 °C | |
ULTEM 9085 | Black, Tan | 47 MPa-33 MPa | 5.8%-2.2% | 153 °C | |
ULTEM 1010 | Amber (Natural) | 64 MPa-41 MPa | 3.3%-2.0% | 216 °C |

Advantages of Fused Deposition Modeling (FDM)
FDM Infill Choices
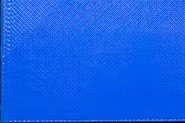
Solid

Light
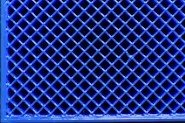
Ultralight
Why choose mXY

Endless choices
Select from a wide range of options for your order, including various materials, finishes, tolerances, markings, and certifications.

User-friendly
Have your parts conveniently delivered to your doorstep, eliminating the need for sourcing, project management, logistics, or shipping.
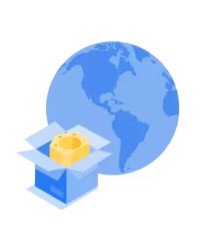
Verified Network
Our certifications include ISO 9001:2015, ISO 13485, and AS9100D. Only the best shops that meet our standards become Suppliers.