Customized Production for the Energy Sector

Accelerate your energy Product Development with MXY
Stay ahead of the curve in the energy sector by collaborating with MXY to streamline your supply chain. Take advantage of on-demand manufacturing services, including 3D printing and CNC machining, to accelerate your product development process.
trusted by
Boost your Energy Supply Chain
with On-Demand Manufacturing
With the rapid pace of technological advancements in both renewable and traditional energy industries, top producers and equipment manufacturers are partnering with Xometry to establish a flexible supply chain using its cutting-edge on-demand manufacturing platform. By leveraging this platform, companies gain access to extensive production capacity across various manufacturing capabilities, including 3D printing, CNC machining, and injection molding, all in one place. This enables them to significantly reduce product development timelines and stay ahead in the market.
Applications in the Energy Sector
Experience the benefits of end-use production of components with high-precision tolerances. Our specialized services also include customized small production runs for repairs or replacement, ensuring that you have the exact parts you need when you need them. Additionally, we offer rapid tooling, jigs, brackets, and chassis for manufacturing, as well as custom tooling to meet your unique requirements. With our advanced technologies, such as 3D printing with metals and plastics, and CNC milling and turning, we can rapidly prototype parts to perfection. Our expertise extends to custom fixturing, fit check gauges, and composite tooling. Trust us to deliver top-notch solutions for all your manufacturing needs.


Explore Our Energy Products Manufacturing Capabilities
Anodizing, passivization, electroplating, powder coating, insert installation, and heat treatment are all common surface treatment processes used in various industries to enhance the properties of materials. Each method offers unique benefits and is chosen based on the specific requirements of the application. Anodizing, for example, creates a protective oxide layer on metals, while powder coating provides a durable and attractive finish. Passivization helps prevent corrosion, and electroplating adds a layer of metal to improve conductivity or appearance. Insert installation ensures secure fastening, and heat treatment alters the material’s properties through controlled heating and cooling processes.
Why choose mXY

Endless choices
Select from a wide range of options for your order, including various materials, finishes, tolerances, markings, and certifications.

User-friendly
Have your parts conveniently delivered to your doorstep, eliminating the need for sourcing, project management, logistics, or shipping.
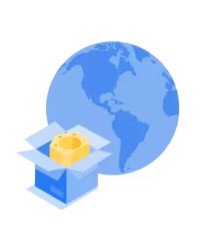
Verified Network
Our certifications include ISO 9001:2015, ISO 13485, and AS9100D. Only the best shops that meet our standards become Suppliers.
The process of placing an order with us
Submit CAD file
Please upload your part design securely to our online quoting tool.
Confirm specs
Customize your part specifications and choose a lead time that aligns with your timeline.
Receive instant quote
Lorem ipsum dolor sit amet, consectetur adipiscing elit. Aenean diam dolor, accumsan sed rutrum vel, dapibus et leo.
Manufacturing
Production kicks off right away
Quality assurance
We fully commit to ensuring that your parts are produced in accordance with our quality criteria.
Shipping
FAQ's
Explore our other production capacities

CNC Machining
Milling, Turning and Post Processing
Tolerances as low as ±.0008 in (0.020mm)
Lead durations 5 business days

3D Printing
FDM, SLA, SLS, MJF
± 0.3% starting from ± 0.3 mm (0.012 in)
Lead durations 1 business days

Injection Molding
Prototypes and production tooling
Diverse array of part intricacies and scales
1 to 2M parts