
Die Casting Services
Get your die casting prototypes and production parts delivered within days
Custom Die Casting Services
MXY is the leading expert in delivering top-notch die casting services. Our team excels in producing highly engineered die casting parts that are utilized in a wide range of durable goods. From machinery and equipment to cars, trucks, and trains, our products are found in approximately 90 percent of these items. Additionally, our die casting parts are also used in various other industries such as defense, medical, aerospace, and even in the creation of art and jewelry. With our commitment to quality and precision, we ensure that our die casting services meet the highest standards in the industry.

Die Casting Process
The process of die casting comprises the injection of liquefied material under high pressure into a mold. The die casting process consists of the following steps:
- Mold Preparation: The mold is made from high-quality steel and is coated and lubricated to aid the part ejection process.
- Injection: The molten material (which is usually aluminum, magnesium, or zinc) is injected into the mold cavity at high pressure.
- Cooling: The molten material hardens within the mold.
- Ejection: The part is ejected from the mold once it has solidified.
- Trim: The part is trimmed, removing any excess material or flash.


Die casting applications
The applications of die casting are found in a variety of industries due to the complexity and detail achievable in each part. Common applications of die casting include:
- Automotive: Engine parts, transmission cases, and structural parts.
- Electronics: Housings, connectors, and heat sinks.
- Consumer Goods: Furniture hardware, appliances, and tools.
- Aerospace: Aircraft components and structural parts.
Advantages of die casting
Die casting offers numerous benefits that have made die casting a popular choice in many manufacturing applications. The advantages of die casting include the following:
- High Precision: Castings can be produced with very close tolerances and dimensions.
- Surface Finish: Castings have a good surface finish and require little post-finishing.
- Strength: Parts are usually stronger than sand cast parts.
- Cost-Effective: High production rates can be achieved due to high āpullā on the mold and getting a good surface finish at the same time; most post-finishing can be eliminated.
- Versatile: Die castings can be produced in virtually any shape.
disadvantages of die casting
Although die casting is a highly desirable method of production, it also has some limitations that need to be taken into consideration when designing parts. Limitations include:
- High initial costs: Die casting is most cost-efficient in medium to high production quantities ā they have faster production rates.
- Design restriction: Some geometry limitations can be a downfall to this method of production.
- Material flow: We always design so material will flow into the farthest reaches of a cavity or mold. The complexity and design of dies are not always successful.
- Porosity: Not all materials are pore free after casting and, if sealed, without normal post-cast tears or impurities.
Our Injection Molding Capabilities
Services | Details |
---|---|
Materials | Our inventory boasts a massive selection of plastic materials available for immediate purchase. |
Choices for Inspection and Certification | Incorporates FAI and PPAP. Compliant with ISO 9001, AS9100, ISO 13485, UL, ITAR, as well as ISO 7 and 8 standards for Medical Clean Room molding. |
Mold Cavity Tolerances | Tolerance of ± 0.0004″ is applied during the mold machining process, with an added tolerance of ± 0.002″ per inch accounted for when considering shrinkage. |
Mold Ownership | Mold maintenance for customer-owned equipment is provided. |
Key Feature Tolerances | Requesting tighter tolerances can lead to an increase in tooling costs due to the need for additional sampling and grooming. We ensure that critical features are milled to a steel-safe condition. |
Reproducibility of Parts Alignment | +/- 0.0003″ or lower |
Key Feature Tolerances | Requesting tighter tolerances can lead to an increase in tooling costs due to the need for additional sampling and grooming. We ensure that critical features are milled to a steel-safe condition. |
Types of Mold Available | MXY generally manufactures tools in Class 102, 103, and 104, with production grades spanning from Class 105 to Class 101, which is the highest production mold available for steel and aluminum. |
Die Casting Types Available from MXY

Hot Chamber Die Casting
Also called gooseneck casting, the hot chamber die casting process is widely used for casting lower melting point alloys like zinc, magnesium, and lead. In this process, a metal-filled holding pot is heated using a hot chamber die casting machine until it becomes molten. The hot chamber system includes a gooseneck feature that forms a holding chamber within the pot and a nozzle-like pathway connecting to the injection cavity of the die. A plunger above the chamber allows molten metal to fill the chamber from the holding pot. Once the chamber is filled, the plunger lowers and pushes the molten material up the gooseneck into the die cavity. The mold is then held under pressure while the metal cools and solidifies. After the metal has cooled sufficiently, the dies open, and the casted piece is ejected using ejector pins.

Cold Chamber Die Casting
The cold chamber die casting method involves keeping the chamber at room temperature without molten metal. Metal is melted in a furnace and poured into the chamber manually using a ladle. Unlike hot chamber die casting, there is no plunger system in cold chamber die casting. Instead, a ram pushes molten metal into the mold under high pressure until it solidifies. This process is ideal for materials with higher melting points like aluminum.

Die Cast Metal Materials
There are various metal materials to choose from for die casting. The material you select will depend on how you plan to use the product. For example, cast aluminum parts are commonly used in aerospace or automotive applications where corrosion resistance and weight reduction are important. You can find more information about the different types of die casting materials we provide below. If you have a specific material request, please inform us!

Aluminum Die Casting
Aluminum alloys are extensively utilized in the production of die cast parts. The recyclability of aluminum and its user-friendly nature provide significant advantages to suppliers in the die casting industry. In certain cases, a cold chamber casting process may be necessary for aluminum die casting due to its relatively higher melting point. Engineers predominantly opt for cast aluminum parts due to their exceptional strength to weight ratios, dimensional stability, and wide range of finishing options.

Zinc Die Casting
Zinc, being one of the die casting metals, is renowned for its ease of casting. It is commonly employed in hot chamber processes. The molten form of zinc exhibits remarkable fluidity, making it ideal for casting. Additionally, it has a relatively low melting point. The strength and stiffness of zinc enable the production of parts with thinner walls and intricate details, while still maintaining precise tolerances. Moreover, the low melting point of zinc alloys used in die casting ensures that the casted parts cool and solidify rapidly, resulting in the highest production rates among die casting materials. Overall, zinc is a versatile material that performs exceptionally well due to its balanced mechanical and physical characteristics.
Die casting usages
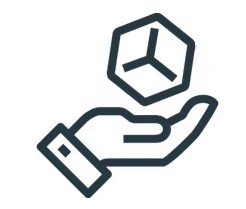
Models Depicting Concepts
Product developers can easily produce physical prototypes of their designs using plastic 3D printing, thanks to its speed and versatility in the iterative process.
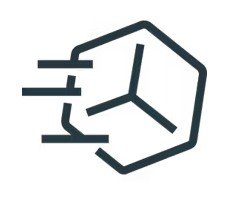
Rapid Prototyping
Plastic 3D printing enables the production of functional plastic prototypes, including moving parts and all-in-one assemblies.
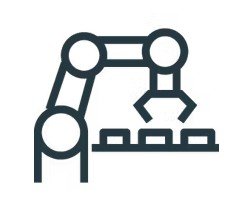
Digital Production Directly
Plastic 3D Printing is perfect for creating numerous customized or individual parts due to its exceptional precision and reliability.
Die Casting Finishes
Why choose mXY

Endless choices
Select from a wide range of options for your order, including various materials, finishes, tolerances, markings, and certifications.

User-friendly
Have your parts conveniently delivered to your doorstep, eliminating the need for sourcing, project management, logistics, or shipping.
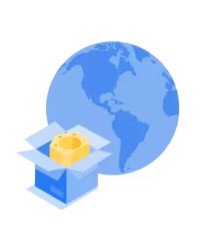
Verified Network
Our certifications include ISO 9001:2015, ISO 13485, and AS9100D. Only the best shops that meet our standards become Suppliers.
The process of placing an order with us
Submit CAD file
Please securely upload the design of your part to our online quoting tool.
Confirm specs
Tailor your part specifications and select a lead time that fits your schedule.
Receive instant quote
Get an accurate quote after our experts evaluate your drawing.
Manufacturing
Production kicks off right away.
Quality assurance
We fully commit to ensuring that your parts are produced in accordance with our quality criteria.
Shipping
Your order will be waiting for you at the entrance.