Aluminum CNC Machining Parts Services
Get your aluminum cnc machining parts and prototypes delivered within days
get your Aluminum CNC Machining parts budget-friendly quote now

Aluminum CNC machining parts on-demand expertise at MXY
High-Quality Aluminum CNC Machining Services
Aluminum CNC machining with its accuracy, efficiency, and dependability, is an essential service for many different sectors. Whether you want large-scale manufacturing, small quantities, or prototypes for your aluminum parts, our services provide customized solutions. Here are some benefits of using aluminum and what our CNC machining services can provide:.
Our advanced CNC machines can produce a broad variety of customized aluminum CNC machining parts, from straightforward workholdings to complex shapes. In addition to being competent with a range of CNC mills and turning centers, our skilled workforce can also provide EDM and grinding services upon request. Because of our precise engineering, we can achieve tolerances as low as +/- 0.0001, ensuring the highest level of accuracy. In addition, with our efficient production process, we may complete your orders in as little as 7 working days.

high-quality aluminum CNC machining parts

Why Choose Aluminum for CNC Machining Parts?
Aluminum is a preferred material for CNC machining parts due to its unique combination of properties that make it ideal for a wide range of applications. Here are some reasons why aluminum is an excellent choice for CNC machining parts:
1. Lightweight yet Strong
Aluminum is known for its lightweight properties, making it easy to handle and transport. Despite its low density, aluminum offers a high strength-to-weight ratio, providing the necessary strength and durability for many applications without adding unnecessary weight.
2. Excellent Machinability
Aluminum is one of the most machinable metals, allowing for faster and more efficient production processes. It can be easily cut, drilled, and milled, resulting in shorter production times and lower manufacturing costs. This is particularly beneficial for complex and high-precision parts.
3. Corrosion Resistance
Aluminum naturally forms a protective oxide layer that prevents corrosion. This makes it suitable for use in environments where exposure to moisture and other corrosive elements is a concern. Anodizing can further enhance its corrosion resistance and provide a range of color options.
4. Thermal Conductivity
Aluminum has excellent thermal conductivity, which is crucial for applications requiring heat dissipation, such as heat sinks and electronic enclosures. Its ability to efficiently transfer heat helps maintain optimal operating temperatures and prolongs the lifespan of components.
5. Cost-Effective
Compared to other metals, aluminum is relatively affordable and widely available. Its cost-effectiveness, combined with its machinability and lightweight properties, makes it a popular choice for CNC machining parts in various industries, including automotive, aerospace, and electronics.
6. Recyclability
Aluminum is 100% recyclable without losing its properties. The recycling process requires only a fraction of the energy needed to produce new aluminum, making it an environmentally friendly choice. Using recycled aluminum can also reduce material costs.
7. Versatility
Aluminum alloys come in a wide range of grades, each offering specific properties suited for different applications. Whether you need high strength, good formability, or excellent corrosion resistance, there is an aluminum alloy that meets your requirements.
Our CNC Machining Capabilities:
CNC Turning, CNC Milling and Wire EDM Machining
Aluminum Alloys We Work With for CNC Machining Parts
When it comes to CNC machining parts, aluminum is a preferred material due to its excellent machinability, lightweight, and corrosion resistance. We work with a wide range of aluminum alloys to meet diverse industry requirements and applications. Here are some of the most common aluminum alloys we utilize in our CNC machining processes:
1. Aluminum 6061
- Properties: Excellent mechanical properties, good corrosion resistance, and versatility.
- Applications: Widely used in aerospace, automotive, and structural components due to its strength-to-weight ratio.
2. Aluminum 7075
- Properties: High strength, excellent fatigue resistance, and good machinability.
- Applications: Ideal for aerospace and military applications where high strength is crucial.
3. Aluminum 2024
- Properties: High strength and excellent fatigue resistance, but lower corrosion resistance compared to other alloys.
- Applications: Commonly used in aerospace applications, especially in the manufacture of fuselage and wing structures.
4. Aluminum 5052
- Properties: Good corrosion resistance, formability, and weldability.
- Applications: Suitable for marine, automotive, and fuel tank applications.
5. Aluminum 6063
- Properties: Excellent corrosion resistance and surface finish; good formability.
- Applications: Commonly used in architectural applications, such as window frames and door frames.
6. Aluminum 6082
- Properties: Good mechanical properties, excellent corrosion resistance, and weldability.
- Applications: Often used in structural applications, including bridges, cranes, and transport applications.
7. Aluminum MIC-6 (Cast Plate)
- Properties: Very stable and stress-relieved; excellent for precision machining.
- Applications: Ideal for tooling, jigs, and fixtures.
Applications of aluminum CNC Machining parts
CNC machines, on the other hand, can be used in a wide range of applications, including metals, plastics and composites. This means that CNC machines can be used for a wide range of applications, from one-off prototyping to bulk production. The advantage of CNC machining is its repeatability, which means it can be used to produce precisely hard parts with high finishes and high tolerances, as well as greater machinability, reducing risk of human error and enabling continuous operation with high supervision.
Industries we serve for aluminum CNC machining parts include:

Automotive
Key components such as CNC-machined ABS bumpers, PC/ABS dashboards, and precision automotive parts such as reflectors, lenses, steering components, engines, and transmissions.

Robotics
Parts for robotics and automation, including manipulator segments, actuators, end tools, motors, automated control systems, grips, and protective casings.

Medical & dental
Medical needs include metal orthopedic plates, prosthetics, ventilators, handheld devices, diagnostic tests, anatomical imaging, surgery equipment, dental implants, orthodontic appliances, crowns, and bridges in both general and specialty areas.

Aerospace & aviation
Aerospace engines, aircraft craft, turbines, brakes, tire parts, lighting systems, vacuum pumps and fuel pump parts.

Consumer Products
Drone parts, Electronic housings, conveyors, fasteners, connectors, generator parts, fixtures, and mechanical and instrument parts for mechanical equipment.

Industrial
Electronic housings, conveyors, fasteners, connectors, generator parts, fixtures, and mechanical and instrument parts for mechanical equipment.

Education
Realistic models can be developed for educational needs using testing tools such as industrial prototypes. MXY works with universities worldwide.

Energy
Energy performance components such as heat exchangers, valves, pipes, pumps & accessories, hydraulic components, battery parts, solar panel components, frames, and impellers.

Lighting
A wide range of cover and back plate, temperature drop, Cut the plates off, flanged mouthpiece, End cap, Suspended ceiling light fixture, Recessed lamp wrap, Plate-mounted ceiling light, LED lighting wrap and Light coverage Metal lamp wrap.
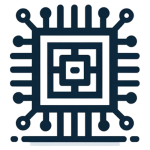
Electronics
Quick tools, custom tools, brackets, and chassis for manufacturing, custom fixturing, Enclosures, injection molding using low-volume prototypes, pilots, or temporary production support, urethane casting, 3D printing and metal.

Hardware startups
We have CNC machining equipment for professional 3D printing, injection molding, sheet metal fabrication and rapid prototyping. Elimold is great at helping startups speed up their conceptualization and can help you do the same.
Advantages of Aluminum CNC machining parts ordered from MXY
CNC machining is a game-changer in the contemporary, fast-paced manufacturing business. If you are working in aerospace, automotive, medical, or any other field that requires high-precision components, CNC should be your go-to option. Here are the reasons why MXYās aluminum CNC machining parts should be your first choice in manufacturing. First of all, there is unparalleled precision and consistency. All the CNC machines are programmed to produce items to exact measurements, and no errors are to be expected. As a result, the highest degree of accuracy is achieved, eliminating errors and ensuring that your designs are flawlessly realized. In turn, this allows us to achieve consistent product quality with no or minimal defects. Secondly, CNC machines allow for faster production. Due to the lack of need for rest and round-the-clock operation while maintaining quality, project completion is significantly accelerated. Third, custom CNC machining parts allow for less costly manufacturing. Due to the highly precise cutting approaches, fewer raw materials are wasted, which saves money. Moreover, decreased manual involvement means less money is spent on labor, which reduces the cost to the client.
Precision and Accuracy
Exceptional Product Quality
CNC machining offers unmatched accuracy when producing all its components. At MXY, for instance, the software-programmed CNC machines are used to draft and cut the exact sizes and dimensions to reduce inaccuracy. Additionally, all constituents are processed similarly and cannot, therefore, lead to any inconsistency. These accurate dimensions eventually translate into quality, reducing the rate of defects in the final product.
Efficiency and Speed
Fast Turnaround Times
Custom CNC machining facilitates increased production speed and efficiency. Consequently, our CNC machines can run non-stop 24/7 without destroying quality. As such, our production potential is relatively high. Indeed, we get less downtime and more productivity, enabling us to meet large orders within tight deadlines.
Materials
Material Versatility
We boasts that its products are close to the same, irrespective of the difference in individual units that can be produced in the thousands. Our strict quality control system and intelligent selective control guarantee each piece has the same quality at the end of its batch, even for the toughest industries such as automotive and aerospace.
Advanced CNC milling Solutions
Complex custom CNC Machining Capabilities
MXY uses advanced multi-axis machining modules in its CNC machines, such as 3/4/5/10-axis custom CNC milling machines and 10/20/40/100 high-speed machining configurations. With such a wide range of axes, MXY can produce parts with complex geometries and varying designs that might prove to be difficult for other CNC milling services. The multiple-axes configuration ensures that MXY is versatile enough to handle very sophisticated projects that require perfect dimensional and shape accuracy.
Customization and Flexibility
Adaptable Manufacturing Solutions
Custom CNC machining parts are highly versatile and can be made with most materials, whether they are metal, plastic, or composite. MXY applies this capability to be able to serve multiple industries with distinct specifications. The CNC machine can produce more convoluted shapes and detailed designs which are otherwise difficult or impossible. Consequently, it is easier for the company to take on custom and unconventional jobs.
Cost-Effective Production
Reduced Labor Costs and Waste
Manufacturing is a question most concerned with price. Custom CNC machining, which uses MXY, diminishes material waste by cutting down with high precision and shaping, meaning that the usage of raw materials is optimized. We also automate many CNC processes, which is why there is less need for manpower in manual work. Reduced material overuse and workforce expenses lead to MXY being able to offer our clients more competitive prices.
Safety and human errors
Enhanced Safety and Reduced Human Error
Safety comes first, which has been the mantra in any manufacturing setup. CNC machines contribute exponentially to safety by minimizing human interference, as most of the machining is automated. Automation means less human error and significantly fewer workplace accidents, as is the case with MXY.
Professional Team
Skilled Technical Support
MXY Custom CNC Machining Services assures customers in all design stages, including but not limited to initial design consultations and final project deliverance. The team has experienced engineers and technicians who can offer insights and assistance in the process to evaluate and improve CNC machining the productās design.
In search of high-quality aluminum CNC machining parts?
Materials for Custom CNC Machining parts
Material | Available |
---|---|
Aluminum | All grades |
Brass/Bronze | All grades |
Copper | All grades |
Plastics | All grades |
Steel | All grades |
Titanium | All grades |
Invar | All grades |
Glass-filled polymer | All grades |
Cemented carbide | All grades |
Carbon steel | All grades |
Monel | All grades |
mild steel | All grades |
Zinc | All grades |
Tolerances and Standards for aluminum CNC Machining Parts
Description | Standard Tolerance |
---|---|
Maximum Size Limit | Machined components with dimensions of up to 2,035 mm x 1,225 mm x 620 mm. |
Accurate tolerances | We have the capability to produce and examine with precise tolerances, which include tolerances as tight as +/- 0.0001″ as per the specifications. |
Distance Measurements | Dimensions (Length, width, and height) and placement (position, concentration, and symmetry) within +/- 0.005 inches. |
Minimum Dimension | The thickness is 0.020 inches (0.50 mm), which could differ based on the geometry of the part and the material selected. |
Finishes | The default finish is machined to 125 Ra or higher. Different finishing choices are available upon request for a quotation. |
Threads and Tape Holes | We have the capability to accommodate all standard thread sizes. Additionally, we are able to create custom threads through machining, although this will necessitate a manual quote review. |
Orientation and Shape Measurements. | For sizes up to 12ā³, the tolerance is +/- 0.0005ā³ and angularity is within 1/2 degree. For sizes 24 and above, contact MXY consult team. |
Critical Condition | Ensure that all sharp edges are automatically smoothed and deburred. Any critical edges that need to remain sharp must be clearly indicated on the print. |
cNC Machining Applications
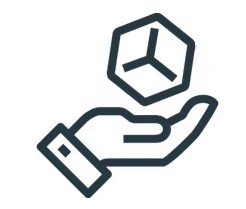
Models Depicting Concepts
Product developers can easily produce physical prototypes of their designs using plastic 3D printing, thanks to its speed and versatility in the iterative process.
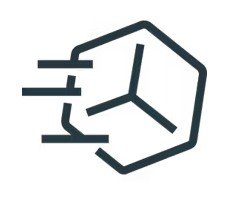
Rapid Prototyping
Plastic 3D printing enables the production of functional plastic prototypes, including moving parts and all-in-one assemblies.
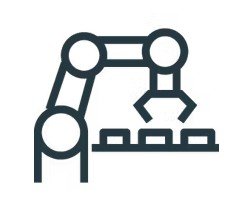
Digital Production Directly
Plastic 3D Printing is perfect for creating numerous customized or individual parts due to its exceptional precision and reliability.
Exhibition Of customized CNC Machining parts
Common aluminum CNC Machining parts Surface Finishes
Brushing
Brushing is a technique that utilizes abrasive pads or brushes to add a finish to the surface of a material. It is commonly used on metal surfaces to enhance their visual appeal. This method is especially effective on stainless steel, creating either a linear or circular pattern on the surface.

Passivation process
Passivation is a common process used to enhance the corrosion resistance of stainless steel by removing iron impurities and forming a protective oxide layer. This helps to improve the durability and performance of stainless steel in tough environments.

Painting
Paint serves as a surface coating that is effective on a wide range of materials, offering both aesthetic enhancement and protection against corrosion. It is available in numerous color options, making it suitable for application on metals, polymers, wood, and various other substrates.

polishing
Enhance the shine and smoothness of your materials by utilizing polishing techniques. By using abrasives such as buffing wheels or polishing chemicals, you can elevate the reflectivity and overall aesthetic of metals, resulting in a stunning mirror-like finish.

Alodine Coating
Alodine coating, also known as chromate conversion coating, is widely used on metals like aluminum. It serves as an excellent primer for paint or powder coatings, providing a durable and corrosion-resistant finish. By creating a thin layer of protection, it enhances the bond between subsequent coatings, ensuring long-lasting results.

More Common aluminum CNC Machining parts Surface Finishes
As-Machined
Brushing is a technique that utilizes abrasive pads or brushes to add a finish to the surface of a material. It is commonly used on metal surfaces to enhance their visual appeal. This method is especially effective on stainless steel, creating either a linear or circular pattern on the surface.

Black Oxide Coating
Black oxide coating is a popular choice for enhancing the surface of steel and iron. This finish not only provides a visually appealing dark surface, but also offers excellent wear resistance. Additionally, the black oxide coating can enhance the lubricity and durability of the treated surface, making it an ideal option for various applications.

Anodizing
Anodizing, a commonly used surface treatment for aluminum, creates a protective oxide layer on the metal’s surface. This not only enhances the durability and corrosion resistance of CNC machined parts but also adds to their visual appeal. Moreover, anodizing offers various options for coloring, making it an ideal choice for enhancing the overall aesthetic of the material.

Powder Coating
Powder coating is an exceptional dry finishing method that utilizes electrostatic application of fine powder onto various surfaces. Once applied, the curing process takes place to guarantee a permanent treatment. With its remarkable ability to withstand impact, solvents, and UV radiation, powder coating provides an enduring and superior finish. From metals to polymers and even wood, there is a wide range of materials that can benefit from the protective coating of powder.

benefits of customized aluminum CNC Machining parts
Accuracy | MXY provides precise tolerances between +/-0.0001ā³ and 0.0005ā³, based on customer requirements. |
Material Choices | MXY offers a convenient solution for material selection, providing you with one-stop options to choose from based on your specific requirements. |
Customized Finishes | Select from a variety of finishes offered for every kind of material part. |
Quick turnaround | MXY Utlizes advanced CNC machines to manufacture precision parts with exceptional accuracy and rapid turnaround times, delivering them in as little as 24 hours. |
Grand scale | CNC Machining is the ideal solution for manufacturing quantities ranging from 1 to 100,000 precision CNC-machined parts. |
Why choose mXY?

Endless choices
Select from a wide range of options for your order, including various materials, finishes, tolerances, markings, and certifications.

User-friendly
Have your parts conveniently delivered to your doorstep, eliminating the need for sourcing, project management, logistics, or shipping.
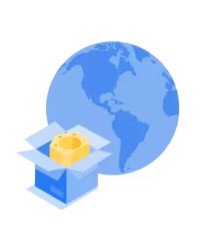
Verified Network
Our certifications include ISO 9001:2015, ISO 13485, and AS9100D. Only the best shops that meet our standards become Suppliers.