Custom Plastic Fabrication Services
Get your Plastic Fabricated prototypes and production parts delivered within days
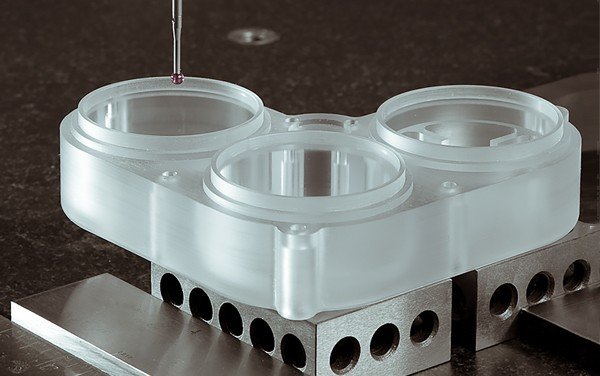
Processes and tooling for Plastic Fabrication
Plastic fabrication involves the shaping, forming, or bonding of plastic sheets, tubes, rods, or bars. It does not involve melt processing methods such as injection molding. The process usually begins with consulting an expert to define the specific requirements of the part. The initial design is then analyzed to ensure it complies with DFM guidelines. Understanding the operating conditions is crucial to selecting the most suitable type of plastic for the application. Factors like operating temperature, chemical exposure, and load cases must be taken into account. Once these considerations are made, the design is finalized and fabrication drawings are created.
Various fabrication techniques and tools are available depending on the design. Some of the most common techniques include:
- CNC Machining: Plastic machining is a quick process that does not cause excessive wear on tools, unless the plastics contain carbon or glass particles. It is important to maintain sharp cutting tools to prevent heat build-up during cutting.
- Welding: Plastic welding is commonly carried out using a specialized extrusion welding tool that generates hot air. The plastic is fed into an extruder, melted, and pushed out through a nozzle. Operators can join plastic components using fillet or butt welds, creating a strong bond with the base material. Other methods like ultrasonic welding are also used to fuse plastic components together.
- Bending: Most plastics can be bent, although some may require heating to bend easily. This is particularly beneficial for more brittle plastics like acrylic.
- Routing: Plastic can be shaped using a router similar to how wood routers are used. Chamfers, rounds, and pockets can be cut, but caution is needed to prevent the plastic from melting due to high-speed rotary tools.
- Drilling: Plastics are easily drilled, but it is crucial to keep drill bits sharp and maintain a relatively slow speed. Dull drills and high speeds can cause the plastic to melt instead of drilling through it.
- Sawing: Various sawing tools like jigsaws, circular saws, band saws, and table saws are available for cutting plastic. It is essential to use purpose-made cutting blades with coarse tooth spacing to ensure clean cuts.
- Thermoforming: Plastic sheets can be molded over different shapes by heating the plastic and draping it over a form. Applying a vacuum helps force the heated plastic over the shape.
- Quality Inspections: Before releasing the component, rigorous quality checks are conducted to ensure it meets strict standards. Inspections typically involve material checks, dimensional checks, and general visual inspections.
adantages of Plastic Fabrication
Plastic manufacturing provides a variety of advantages. Here are some of the key ones:
- Customization
- Light Weight
- Cost-Effectiveness
- Versatility
- Energy Efficiency
- Implementation Simplicity
- Low Friction
- Chemical Resistance
Customization
Manufacturers demonstrate their expertise in adapting their products to suit the unique requirements of various projects and industries. This level of customization goes beyond simple alterations in dimensions and form, as they are also capable of modifying the material characteristics of plastic sheets to cater to a wide range of applications. Through the customization of sheets for the packaging industry, they are able to produce containers that offer optimal safeguarding for packaged goods. By adjusting the thickness and composition of the materials, designers and manufacturers can guarantee that the containers possess the necessary strength to endure the rigors of transportation.
Light Weight
Plastics typically have densities around 1000 kg/m3, with certain types exhibiting strength levels comparable to aluminum. This characteristic makes plastic a suitable choice for industries like aerospace and automotive, where lightweight materials are essential for design purposes.
Cost-Effectiveness
Certain types of plastics, referred to as commodity plastics, offer a cost-effective alternative to metals and other construction materials. The use of standard plastic fabrication methods helps to reduce costs even more by eliminating the need for expensive tooling.
Versatility
Numerous types of plastics are accessible, each offering a diverse set of characteristics. This variety simplifies the process of selecting the ideal plastic for your specific needs. Furthermore, additives can be incorporated into certain plastics to enhance their resistance to UV rays, heat, and chemicals. Apart from their inherent properties, plastics can be molded using a variety of methods.
Energy Efficiency
Extrusion machines in the modern era are engineered to enhance energy efficiency by integrating cutting-edge heating and cooling mechanisms. These machines utilize sophisticated components that effectively melt the pellets, minimizing heat dissipation and guaranteeing accurate temperature regulation. Additionally, the continuous nature of extrusion minimizes the downtime between production runs. The molding process also achieves energy efficiency through innovative heating methods and pressurization techniques. Recent machines are equipped with energy-efficient heaters that swiftly heat the molds to the desired temperature, thereby reducing the time and energy required for molding. Furthermore, the advanced hydraulics and pneumatics in these machines ensure precise control over the pressure applied.
Implementation Simplicity
Plastic sheet fabrication methods, like extrusion and casting, are widely known and understood in the industry. This means that manufacturers don’t need complicated machinery or extensive training. This simplicity in setup and operation allows for faster adoption of the process, reducing initial costs and speeding up time to market. The availability of various plastic materials also makes implementation easier. Plastic sheets can be made from polyethylene, polycarbonate, PVC, and acrylic, each with unique properties for different uses. Manufacturers can choose the most suitable material to ensure the fabricated plastic sheets meet performance standards.
Low Friction
Certain types of plastics, such as PTFE (polytetrafluoroethylene) or UHMWPE (ultra-high-molecular-weight polyethylene), exhibit remarkably low coefficients of friction. As a result, they are exceptionally well-suited for serving as protective and low-friction liners within metal chutes, particularly in the context of bulk materials handling applications.
Chemical Resistance
Certain plastics are capable of withstanding highly corrosive chemicals, unlike metals which would corrode rapidly. This quality makes these specific plastics perfect for harsh environments, such as those commonly found in chemical processing facilities.
Mold-Tech finishes Reference
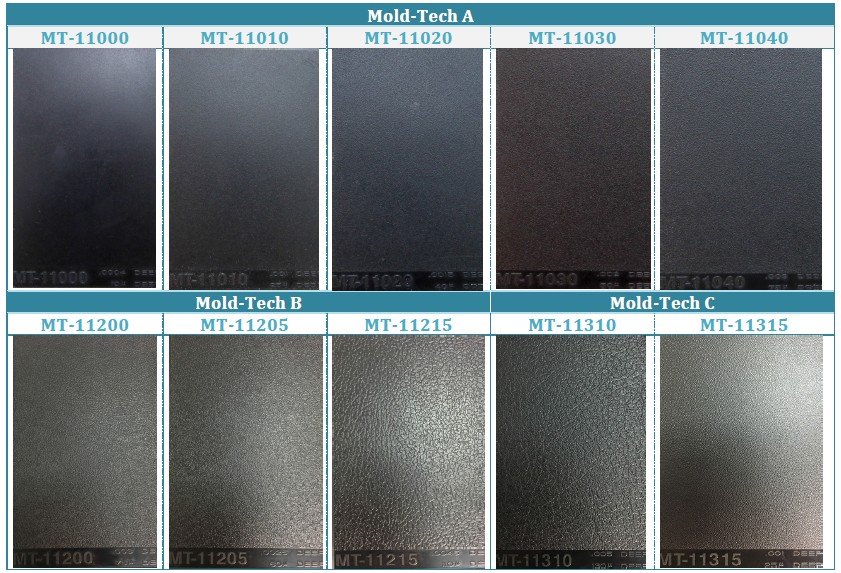
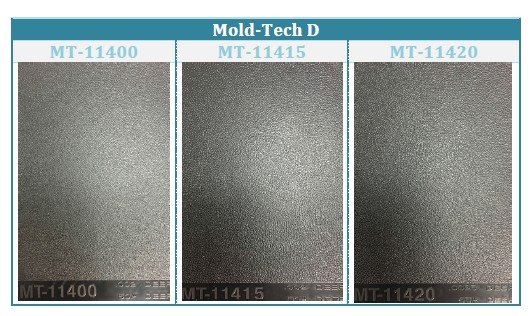
Plastics Industry Association (SPI) Mold Finishes
Standard SPI Injection Molding Finishes
Finish | Mold Finish Description | Description | SPI Standard | Comments | Surface Roughness, Ra(um) |
Glossy | #3 Diamond Polish | The mold is first smoothed and then polished with a diamond buff. | A-1 | Mirror-like Finish | 0 – 1 |
#6 Diamond Polish | A-2 | 1 – 2 | |||
#15 Diamond Polish | A-3 | 2 – 3 | |||
Semi-Glossy | #600 Grit Paper | The mold is smoothed with fine grit paper. | B-1 | Fine surface Finish | 2 – 3 |
#400 Grit Paper | B-2 | 4 – 5 | |||
#320 Grit Paper | B-3 | 9 – 10 | |||
Matte | #600 Grit Stone | The mold is smoothed with fine grit stone. | C-1 | Removing all machining marks | 10 – 12 |
#400 Grit Stone | C-2 | 25 – 28 | |||
#320 Grit Stone | C-3 | 38 – 42 | |||
Textured | #11 Glass Bead | The mold is first smoothed with fine grit stone and then sandblasted with different medias. | D-1 | Resulting in a textured surface. | 10 – 12 |
#240 Aluminium Oxide | D-2 | 26 – 32 | |||
#24 Aluminium Oxide | D-3 | 190 – 230 | |||
As-Machined | – | The mold is finished to the machinist’s discretion. | – | Visible tool marks | Canbe down to 0.8 or up to 32 |
SPI finishes Reference

VDI finishes
VDI surface finishes are defined by the texture standard established by Verein Deutshcher Ingenieure (VDI), the Society of German Engineers. These finishes are typically achieved through the EDM (Electrical Discharge Machining) process during mold machining. Alternatively, similar finishes can be achieved using the “Mold-Tech” style. EDM is commonly employed for smaller areas, while “Mold-Tech” is more suitable for larger areas.
VDI | Draft angle – °per side | ||||
VDI # | Ra (um) | Rz (um) | ABS | PC | PA (Nylon) |
12 | 0.4 | 1.5 | 0.5Ė | 1Ė | 0Ė |
15 | 0.56 | 2.4 | 0.5Ė | 1Ė | 0.5Ė |
18 | 0.8 | 3.3 | 0.5Ė | 1Ė | 0.5Ė |
21 | 1.12 | 4.7 | 0.5Ė | 1Ė | 0.5Ė |
24 | 1.6 | 6.5 | 1Ė | 1.5Ė | 0.5Ė |
27 | 2.24 | 10.5 | 1.5Ė | 2Ė | 1Ė |
30 | 3.15 | 12.5 | 2Ė | 2Ė | 1.5Ė |
33 | 4.5 | 17.5 | 2.5Ė | 3Ė | 2Ė |
36 | 6.3 | 24 | 3Ė | 4Ė | 2.5Ė |
39 | 9 | 34 | 4Ė | 5Ė | 3Ė |
42 | 12.5 | 48 | 5Ė | 6Ė | 4Ė |
45 | 18 | 69 | 6Ė | 7Ė | 5Ė |
vDI finishes Reference

Valuable Advice for Choosing Surface Finishes
A high level of gloss on a mold does not guarantee the same level of gloss on the injection molded part. This is because there are other factors that come into play, such as the type of material used, the conditions during molding, and the design of both the mold and the part. For instance, when comparing an ABS part to a PP part, the ABS part will have a shinier surface finish.
To achieve a high gloss surface finish, a higher quality mold material is necessary. Tool steels with the highest level of hardness are required in order to achieve a finely polished surface. For example, NAK80 tool steel (HRC 40-43) is needed to produce a mirror-like surface finish, as opposed to P20 tool steel (HRC 30-33). It is important to note that using a harder mold tool will increase both the time required for machining and post-processing, which will have an impact on the overall cost and lead time.
When using glass or other mineral-filled materials, there may be streaking in the material, making it more difficult to produce a highly cosmetic part. However, this is not always the case. It is always advisable to consult with the manufacturer and obtain a material sample plaque of the actual material you plan to use in order to have a better understanding of the surface requirements you are aiming for.
Injection molding Applications
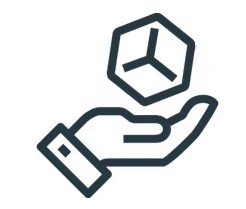
Models Depicting Concepts
Product developers can easily produce physical prototypes of their designs using plastic 3D printing, thanks to its speed and versatility in the iterative process.
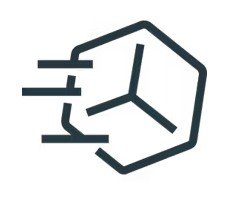
Rapid Prototyping
Plastic 3D printing enables the production of functional plastic prototypes, including moving parts and all-in-one assemblies.
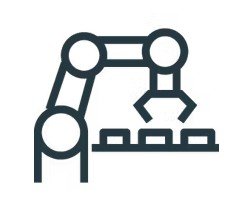
Digital Production Directly
Plastic 3D Printing is perfect for creating numerous customized or individual parts due to its exceptional precision and reliability.
Why choose mXY

Endless choices
Select from a wide range of options for your order, including various materials, finishes, tolerances, markings, and certifications.

User-friendly
Have your parts conveniently delivered to your doorstep, eliminating the need for sourcing, project management, logistics, or shipping.
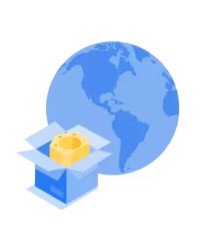
Verified Network
Our certifications include ISO 9001:2015, ISO 13485, and AS9100D. Only the best shops that meet our standards become Suppliers.