
Custom Hydroforming service
Get your Injection Molding prototypes and production parts delivered within days
What is Hydroforming?
Hydroforming is a metal forming technique that utilizes hydraulic fluid pressure to produce seamless metal shapes, unlike stamping and die forming. In this process, a sheet of metal is positioned between a press with a male die element connected to a piston on one side, and a chamber containing hydraulic fluid on the other side. A rubber diaphragm and wear pad are then placed on top of the metal sheet before the press is closed. The chamber is pressurized with hydraulic fluid, causing the piston to push the punch into the pressurized cavity, resulting in a uniform deep-drawn profile matching the shape of the punch.
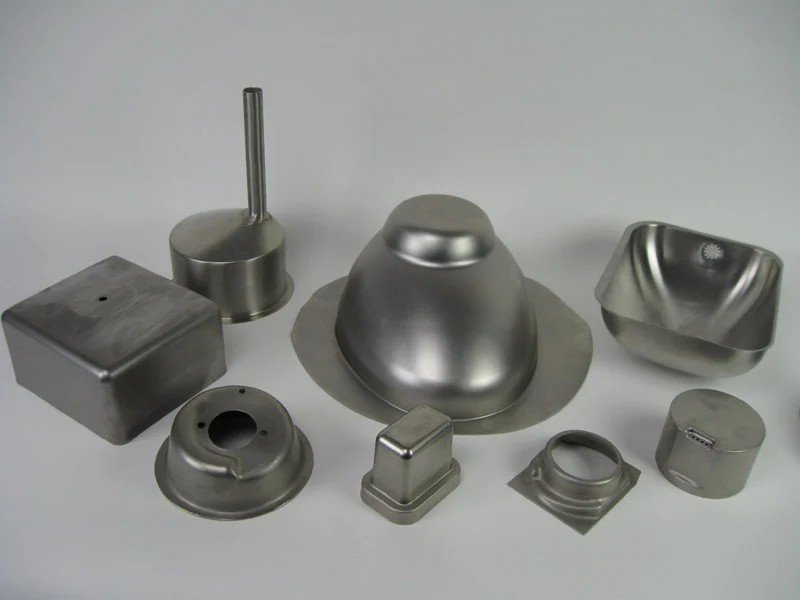
The rubber diaphragm and wear pad prevent scrapes and scratches commonly seen in metal stamping, while also providing support to ensure a consistent surface finish. Once the forming process is complete, the part can be removed from the press and undergo additional processes such as tapping, drilling, and finishing touches.
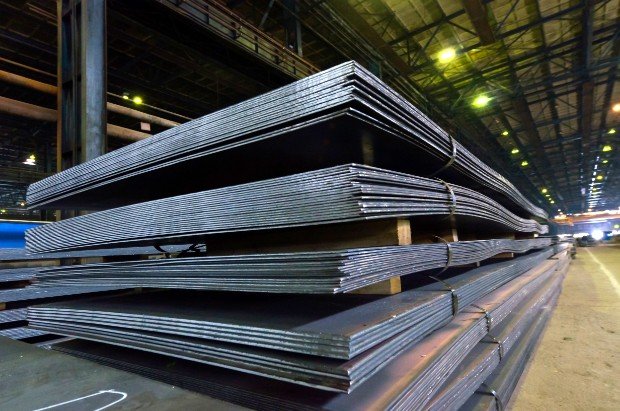
Materials for Hydroforming
- Titanium
- Galvanized Steel
- High Nickel Alloys
- Inconel
- Copper
- Carbon Steel / Stainless Steel
- Bronze
- Brass
- Stainless Steel
- Aluminum
Benefits of Hydroforming Services
- Rapid production
- Precision and consistency
- Large-scale manufacturing

Rapid production
Hydroforming cycle times can range from 30 to 60 seconds, allowing parts to be produced and delivered swiftly. MXY offers rapid turnaround times, delivering parts to customers worldwide in just a few days. Increase efficiency by manufacturing parts with us allowing for better allocation of business resources.
Precision and consistency
Hydroforming is renowned for its exceptional precision and consistency, improving wall thickness uniformity while minimizing defects like shock lines, draw lines, shearing, tearing, and other issues.
Large-scale manufacturing
Hydroforming is a perfect manufacturing process for high-volume part production. MXY’s hydroforming services cater to larger designs with hundreds of parts and smaller designs with thousands of parts, helping designers recover their upfront tooling and design expenses.
Forming Shapes with Hydroforming
MXY utilizes hydroforming to fabricate precision parts with complex shapes including:
- Curves with a parabolic shape
- Elliptical or oval shape
- Square structures
- Multiple layer shapes
- Uneven or non-uniform forms
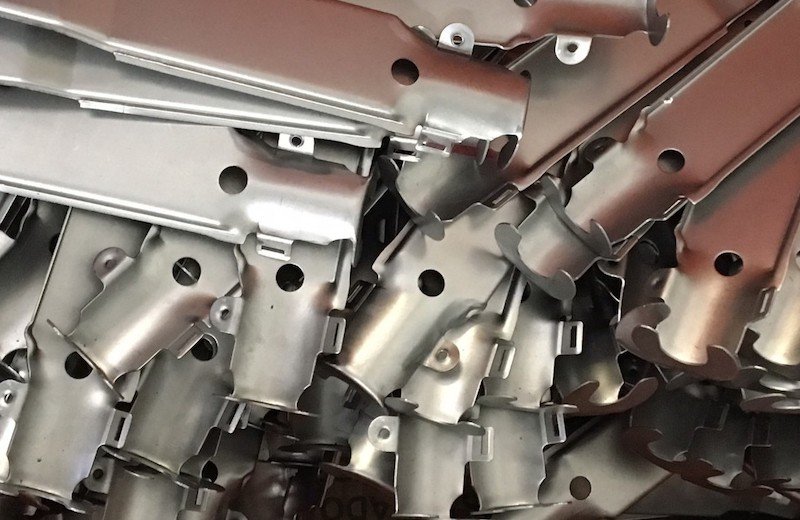
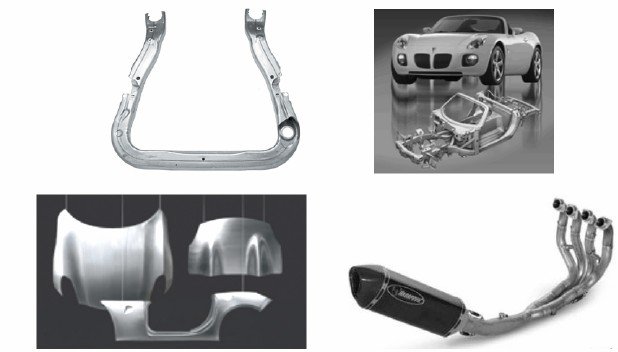
Hydroforming Sector
- Medical Sector
- Industrial Equipment
- Automotive
- Aviation and Space Industry
- Kitchenware
Medical Sector
Hydroforming is a valuable technique for creating intricate designs in medical devices like medical pumps, which rely on sturdy vessels. With our MXY ISO 13485 certification, we can ensure the production of high-precision medical-grade parts that meet the requirements of these challenging products.
Industrial Equipment
Industrial equipment such as air ducts, HVAC equipment, plumbing stock, agricultural components, heat exchangers, and more undergo hydroforming to guarantee compliance with national standards and safety regulations. The precision and dependability of hydroforming guarantee that each piece will maintain uniformity within its manufacturing batch, delivering unparalleled consistency and quality.
Automotive
Hydroforming is widely used in automotive manufacturing for producing large unibody components such as panels and hoods due to its superior quality and repeatability. The resulting parts are stronger and more uniform compared to traditional drawn or stamped metal parts, reducing both cost and the risk of part failure. Additionally, being a cold forming process, hydroforming enables secondary heat treating procedures essential for high-strength applications like car frames and structural components.
Aviation and Space Industry
Hydroforming is a perfect manufacturing process for high-volume part production. MXY’s hydroforming services cater to larger designs with hundreds of parts and smaller designs with thousands of parts, helping designers recover their upfront tooling and design expenses.
Kitchenware
Food processing equipment and food service parts undergo hydroforming to enable manufacturers to incorporate unique design features such as asymmetrical inlet and outlets, piping, and other customization options.
Hydroforming vs. Deep Drawing vs. Metal Spinning
Hydroforming utilizes hydraulic pressure to evenly distribute pressing forces onto metal stock through fluid dies, resulting in the desired shape of the male tooling. It is applicable to a wide range of materials, from mild steel to high temperature alloys and superalloys. This technique is particularly advantageous for creating asymmetrical complex shapes that are challenging or impossible to produce using simpler methods. The highly pressurized fluid in hydroforming enables the production of intricate shapes, allowing hydroforming companies to meet precise specifications and tolerances due to the uniform effects of pressurized fluid shaping.

Sheet metal spinning, also known as metal spinning, is a metal forming technique where a disc of sheet metal is rotated at high speeds and pressed onto an axially-symmetric mandrel in the shape of the end part. The resulting metal shapes are typically less complex and can be created using manual or CNC spinning equipment. These spun metal shapes find applications in decorative, architectural, and furniture industries, as well as in aerospace for making nose cones for rockets and planes. However, it is important to note that metal spinning is not suitable for creating asymmetrical designs. While metal spinning offers minimal tooling costs, the variable cost per-part is higher compared to hydroforming.
Deep drawing, on the other hand, is a cold forming metalworking process that involves forcing a punch through a series of forming dies to create a deep, seamless shape with minimal material loss. This process is best suited for producing simplistic, axially-symmetrical parts and is commonly used in the manufacturing of pressure vessels and tanks that require seamless construction to avoid potential points of failure.
Hydroforming alternatives
If hydroforming is not suitable for your intended application, there are several other common alternatives available.
- Metal Injection Molding
- Die Casting
- Metal Stamping
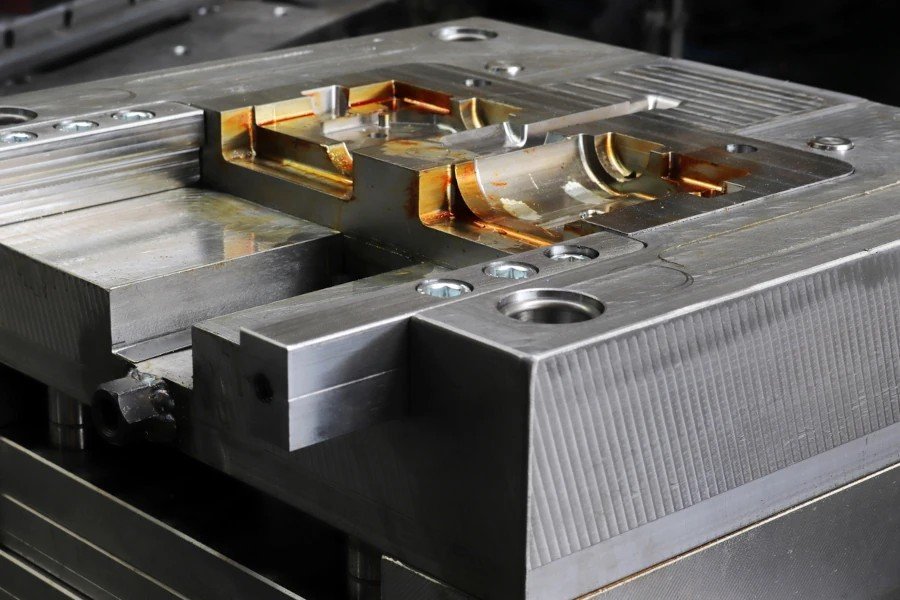
Metal Injection Molding
When it comes to the importance of part size and sharp angles, metal stamping proves to be a cost-effective and extremely versatile manufacturing method for producing angled metal parts. This process allows for the creation of numerous parts in a single workday, featuring intricate angled and deep-drawn shapes with consistent precision. For further information, visit our Metal Stamping Service page.
Die Casting
Die casting is a well-established manufacturing technique that finds extensive application in various industries such as automotive, construction, consumer goods, medical, and more. Its popularity stems from the wide range of materials it can accommodate and its remarkable versatility. For further information, please visit our dedicated page on MXY’s Die Casting Capabilities.
Metal Stamping
Metal injection molding (MIM) is a multi-stage manufacturing process similar to plastic injection molding. It is utilized to create small, intricate metal parts in large quantities. Metal powders are polymerized, injected into molds, de-binded, and sintered to enable mass production using various materials. For additional information, please refer to our MXY Metal Injection Molding Service webpage.
Hydroforming usages
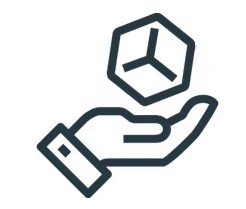
Models Depicting Concepts
Product developers can easily produce physical prototypes of their designs using plastic 3D printing, thanks to its speed and versatility in the iterative process.
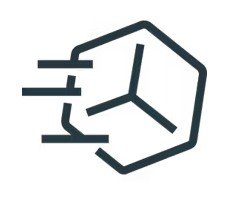
Rapid Prototyping
Plastic 3D printing enables the production of functional plastic prototypes, including moving parts and all-in-one assemblies.
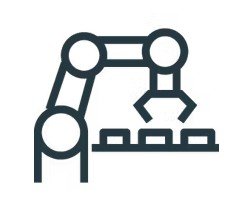
Digital Production Directly
Plastic 3D Printing is perfect for creating numerous customized or individual parts due to its exceptional precision and reliability.
Why choose mXY

Endless choices
Select from a wide range of options for your order, including various materials, finishes, tolerances, markings, and certifications.

User-friendly
Have your parts conveniently delivered to your doorstep, eliminating the need for sourcing, project management, logistics, or shipping.
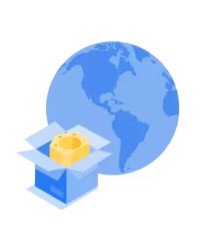
Verified Network
Our certifications include ISO 9001:2015, ISO 13485, and AS9100D. Only the best shops that meet our standards become Suppliers.
The process of placing an order with us
Submit CAD file
Please upload your part design securely to our online quoting tool.
Confirm specs
Customize your part specifications and choose a lead time that aligns with your timeline.
Receive instant quote
Lorem ipsum dolor sit amet, consectetur adipiscing elit. Aenean diam dolor, accumsan sed rutrum vel, dapibus et leo.
Manufacturing
Production kicks off right away
Quality assurance
We fully commit to ensuring that your parts are produced in accordance with our quality criteria.
Shipping
FAQ's
Explore our other production capacities

CNC Machining
Milling, Turning and Post Processing
Tolerances as low as ±.0008 in (0.020mm)
Lead durations 5 business days

3D Printing
FDM, SLA, SLS, MJF
± 0.3% starting from ± 0.3 mm (0.012 in)
Lead durations 1 business days

Injection Molding
Prototypes and production tooling
Diverse array of part intricacies and scales
1 to 2M parts