Surface Grinding Service On demand

What is surface grinding
Overview of Surface Grinding
Surface grinding stands out as a powerful and meticulously managed procedure where a rotating grinding wheel interacts with a workpiece. This grinding wheel, which typically consists of abrasive particles like aluminum oxide, silicon carbide, or carborundum, is fastened to a spindle and spins at high speeds. The workpiece is firmly secured either on a magnetic chuck or within a clamping fixture, and it is brought into contact with the spinning grinding wheel. Although the wheel is primarily set on a horizontal axis allowing its prepared cutting surface to press down onto the workpiece’s top, vertical setups for grinding side faces are also available but less common.

Configuration of Grinding Machines
Most grinding machines feature the grinding wheel on a stationary shaft with vertical movement only (Z direction). Below this, the clamping table for the workpiece slides across the horizontal plane, enabling any part of the workpiece’s upper surface to engage with the grinding wheel.
Alternative Grinding Methods
An alternative method places the workpiece between a grinding wheel and a traction or feed wheel, which drives the workpiece into the grinding wheel. This method is particularly effective as it allows the use of very wide grinding wheels that can remove large sections of material swiftly.
Grinding Dynamics
The abrasive particles on the grinding wheel serve as tiny cutters, methodically wearing down the workpiece through a mix of cutting, plowing, and rubbing actions. The grinding process generates significant heat, which necessitates the use of coolants or other methods to prevent overheating and potential damage to the workpiece.
Maintaining the Grinding Wheel
To keep the grinding wheel in optimal condition, its surface is ‘dressed’ by removing a layer of spent abrasive particles using a diamond bit. This process ensures that the wheel’s face remains flat axially, which is crucial for achieving uniformly flat surfaces on the workpiece with multiple passes.
Metal Types for Surface Grinding Materials
Surface grinding can handle a wide variety of metal materials, each with its unique characteristics that affect the grinding process. Here is a list of metals commonly subjected to surface grinding, along with professional details relevant to the CNC machining industry:

- Aluminum: Known for its softness and susceptibility to clogging the grinding wheel; requires specific grinding techniques to prevent embedding.
- Brass: Similar to aluminum in softness, brass is non-ferrous and thus requires grinding wheels that resist clogging and provide a smooth finish.
- Cast Iron: This material is hard and brittle, demanding a robust wheel such as aluminum oxide for efficient grinding.
- Carbon Steel: It’s widely ground in the manufacturing sector and often uses ceramic aluminum oxide wheels.
- Stainless Steel: Due to its toughness, stainless steel often requires wheels with ceramic abrasives or cubic boron nitride (CBN).
- Tool Steel: This hard material typically requires diamond or CBN wheels for precision grinding, especially after heat treatment.
- Copper: Although it’s a softer, ductile metal, copper can stick to the grinding wheel; silicon carbide wheels can be effective here.
- Titanium: Known for its strength-to-weight ratio, it can be challenging to grind and usually needs specialized wheels to prevent overheating.
- Nickel Alloys: These materials are tough and can be gummy, so they require the use of CBN or ceramic wheels.
- Tungsten Carbide: Extremely hard and often ground with diamond wheels for high-precision requirements.
- Bronze: Similar to brass, it grinds well with aluminum oxide wheels and requires careful handling to avoid loading the wheel.
- Hardened Steel: For hardened steel, ceramic, CBN, or diamond wheels are necessary to handle the high hardness level effectively.
- Inconel: This is a nickel-chromium-based superalloy, known for its resistance to corrosion and oxidation, and is commonly ground with CBN wheels.
- Monel: It is a nickel-copper alloy that is resistant to corrosion and can be more difficult to machine, often requiring CBN for grinding.
- Hastelloy: This nickel-molybdenum alloy is similar to Inconel and Monel in its grinding characteristics and requirements for CBN wheels.
The grinding wheel material and grit size are selected based on the metal being ground. The hardness, thermal properties, and finishing requirements of each metal dictate the appropriate grinding wheel to use. High precision, proper wheel selection, coolant application, and machine settings are essential to achieve the desired surface finish and dimensional accuracy in the final product.
For each material, different types of grinding techniques may be employed depending on the desired finish, including surface grinding, cylindrical grinding, centerless grinding, internal grinding, creep feed grinding, jig grinding, and gear grinding. In professional CNC machining and surface grinding services, experts consider the material’s behavior under different grinding conditions to achieve the necessary specifications.
Metal Types for Surface Grinding Materials
CNC technology for surface grinding provides numerous advantages compared to traditional methods, particularly when precision and efficiency are crucial. Here are a few of the main benefits:

- Precision: CNC surface grinding is highly precise, consistently achieving tolerances that manual methods cannot match. This is particularly crucial in industries like aerospace and medical equipment manufacturing, where components need to meet exact specifications.
- Increased Productivity: Automation in CNC grinding significantly boosts productivity by allowing continuous operation with minimal manual intervention, unlike traditional methods which may require frequent setup changes.
- Versatility: CNC grinders are versatile and can accommodate various shapes, sizes, and material types. They’re capable of handling multiple grinding processes, including intricate and complex shapes required in specialized industries.
- Repeatability: CNC machines can reproduce the same task with high precision repeatedly, ensuring uniformity across mass-produced parts, which is beneficial for quality control.
- Automation: The process reduces human error by automating repetitive tasks, freeing up operators for more complex responsibilities and leading to more consistent outcomes.
- Efficiency: CNC grinding machines can work continuously without breaks, making them faster and more efficient than manual counterparts. They’re also capable of more complex tasks without the need for additional setups.
- Safety: CNC machines have advanced safety features that reduce the risks associated with manual grinding. They can be operated with less direct human interaction, lowering the chances of accidents.
- Flexibility and Quick Setup: These machines can be quickly reprogrammed for different tasks, offering flexibility in a dynamic production environment where the types of parts being produced can change regularly.
- Reduced Waste: The precision of CNC grinding means there’s less material waste due to errors, and the consistency of the process means fewer defective parts, contributing to cost savings and sustainability.
- Environmental Impact: CNC machines are designed with energy efficiency in mind, thus contributing to a reduced environmental footprint in comparison to some traditional methods which may be less energy efficient and generate more waste.
These advantages make CNC grinding a preferred choice for high-precision, high-efficiency manufacturing processes across a range of industries, including aerospace, automotive, medical, and energy sectors. As technology continues to advance, the role of CNC grinding is likely to expand, offering new manufacturing solutions and maintaining high standards of precision and reliability.
Disadvantages of Surface Grinding

Surface grinding, despite being a widely utilized manufacturing process in industries such as aerospace, automotive, and medical for achieving precise dimensions and fine surface finishes, has several disadvantages that can affect its efficiency and effectiveness in certain scenarios:
- Heat Impact: Insufficient coolant supply or cutting too deep can generate excessive heat on the workpiece, affecting its previous hardening. This can be detrimental to the resilience of components like slides and plane bearings.
- Inefficiency for Large Volume Production:Surface grinding is not the most efficient method for removing large volumes of material quickly. This makes it less suitable compared to other machining processes like milling or turning when high material removal rates are required
- Cost Factors:Initial setup and ongoing operational costs for surface grinding can be high. This includes the cost of purchasing and maintaining precision grinding machines and the ancillary systems needed to operate them effectively, such as dust extraction and coolant systems.
Different options for Surface grinding
Surface grinding is a widely used abrasive machining process in which a spinning wheel covered in rough particles (grinding wheel) cuts chips of metallic or nonmetallic substance from a workpiece, making a face of it flat or smooth. This technique is used to produce a high-quality finish on flat surfaces. However, there are several alternative methods that can be used for similar purposes, each with their own advantages and disadvantages depending on the specific requirements of the job. Here are some notable alternatives to surface grinding:
Electropolishing
Electropolishing utilizes an electrochemical process to remove a thin layer from the surface of a workpiece, enhancing the overall quality of the surface finish. While it does not improve flatness, it yields a superior, smooth finish, making it ideal for applications requiring a high degree of polish.
Linishing
Linishing involves the use of an abrasive belt to refine the surface of a workpiece. Although it does not alter the flatness like surface grinding, it can produce a similar visual finish, providing an aesthetically pleasing appearance without extensively modifying the surface contour.
As-Machined Finish
Our CNC milling technology is capable of producing exceptionally flat vertical and horizontal surfaces. While this method may leave machining marks, it ensures a high degree of flatness, suitable for many precision engineering applications.
Grit Blasting
Grit blasting is an effective process for removing superficial layers, offering a distinctive finish that, while not altering the flatness, enhances the surface’s aesthetic appeal. This method is perfect for projects where visual texture is more important than dimensional flatness.
Traditional Flattening Techniques:
Lapping, Honing, Scraping
Lapping, honing, and scraping are time-honored methods for achieving highly flat surfaces, such as those needed in machine tool slideways and precision measurement references. These techniques require considerable skill and can significantly even out irregularities to achieve optimal flatness. The quality of the finish heavily depends on the operator’s expertise.
Additional Techniques
Chemical Milling
Chemical milling uses controlled chemical etching to remove material from the workpiece. This method allows for precise thickness control and is used to create complex shapes with very fine surface finishes, though it is not typically used for improving flatness.
Thermal Deburring
Thermal deburring involves the use of intense heat to remove burrs and imperfections from metal parts. This process is particularly effective for cleaning up small, difficult-to-reach areas that mechanical deburring tools might miss, contributing to a smoother and more uniform surface appearance.
Each of these technologies offers unique benefits to suit different industrial needs. By selecting the appropriate surface finishing technique, you can significantly enhance both the functionality and aesthetic appeal of your parts. For more detailed information or consultation on which method best fits your requirements, please contact our technical support team.
Why choose mXY

Endless choices
Select from a wide range of options for your order, including various materials, finishes, tolerances, markings, and certifications.

User-friendly
Have your parts conveniently delivered to your doorstep, eliminating the need for sourcing, project management, logistics, or shipping.
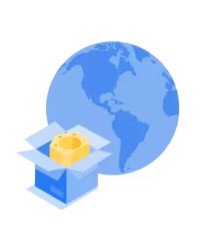
Verified Network
Our certifications include ISO 9001:2015, ISO 13485, and AS9100D. Only the best shops that meet our standards become Suppliers.